The construction world stands at a crossroads, confronted with the dual challenges of escalating housing demands and pressing environmental concerns. Amidst this landscape, a new published report on Modern Methods of Construction (MMC) shines a spotlight on the pivotal role of Australia’s timber frame and truss sector, advocating for an elemental prefabrication approach that promises to redefine building practices.
In recent years, the MMC paradigm has emerged as a game-changer, due largely to its potential to enhance efficiency, reduce costs, increase onsite construction productivity, and significantly lower carbon footprints.
MMC refers to a broad range of construction techniques that incorporate a degree of pre-manufacturing or site-based process enhancements. While many think of MMC as synonymous with fully volumetric or modular construction—essentially pre-constructed homes delivered to the site—it is crucial to clarify that this is not how the bulk of the homes in Australia will be built in the future. It is important to note that the term MMC encompasses a range of offsite prefabrication solutions that can improve the efficiency, effectiveness and productivity of building projects. A very important component of MMC is offsite elemental prefabrication.
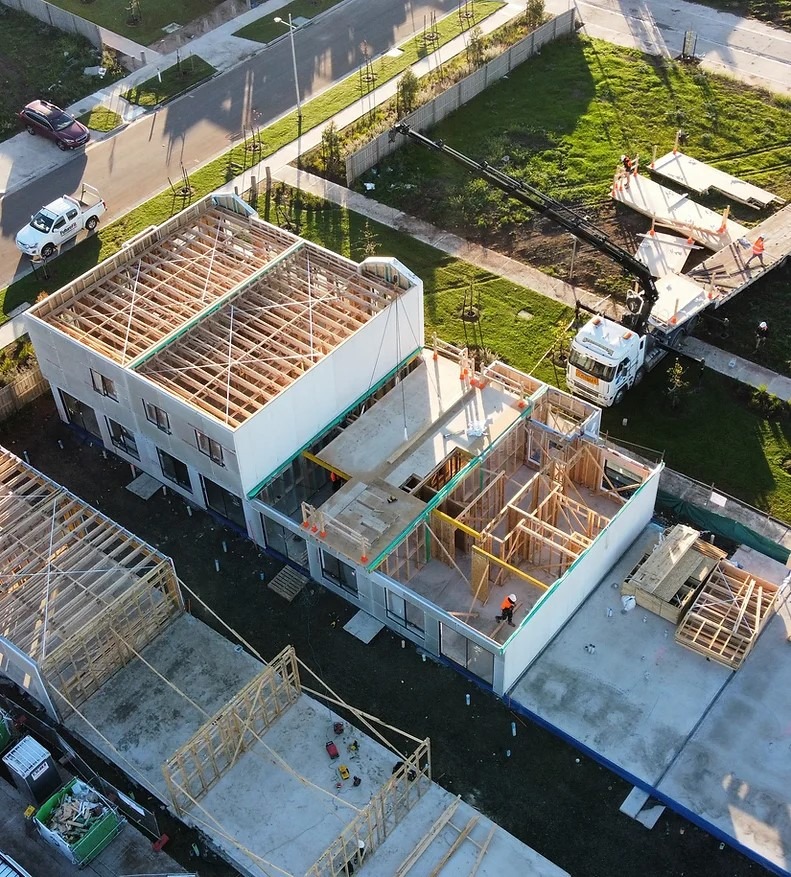
Elemental prefabrication focuses on the offsite production and delivery of high-quality value-added elements, products, and systems, kits-of-parts, all manufactured under controlled factory conditions with these component parts then assembled quickly and efficiently onsite; it’s an approach that certainly leverages the flexibility, adaptability and sustainability of materials like wood.
This method aligns perfectly with Australia’s thriving timber frame and truss sector. Timber, celebrated for its versatility and low embodied energy, is a formidable alternative to more carbon-intensive materials like concrete and steel. The sector’s expertise in crafting lightweight, durable, and eco-friendly timber components provides a critical advantage. Not only does timber construction sequester carbon, helping mitigate climate change, but it also permits greater design flexibility and adaptability to varied architectural requirements.
Additionally, the elemental approach is inherently more resilient and responsive to the dynamic nature of on-site construction challenges. Builders can modify and assemble components according to specific site conditions and project demands, thus avoiding the limitations posed by prefabricated volumetric units. This adaptability is crucial in addressing both urban and regional housing needs, especially in a diverse landscape like Australia.
The report further underscores the economic benefits of bolstering support for the timber frame and truss sector. By investing in local timber production and embracing innovative practices, Australia can enhance its competitive edge in the construction industry while fostering job creation and promoting sustainable practices. This symbiotic relationship between economic growth and environmental stewardship is central to the elemental approach’s value proposition.
The report, Modern Methods of Construction and the Important Role of Australia’s Timber Frame & Truss Sector confidently articulates a transformative vision for the construction sector, where leveraging the strengths of Australia’s timber frame and truss industry through an elemental approach not only addresses current inefficiencies but also charts a sustainable and scalable path forward.
As the Australian building sector seeks construction solutions that are agile, eco-friendly, and financially sound, the elemental prefabrication approach, with a focus on timber, stands as a beacon of innovation and practicality.
FTMA will be hosting a webinar and podcast shortly on this important report, promoting the benefits of an elemental approach to MMC.
For further information on the report, please contact Kersten Gentle, FTMA CEO on 0418 226 242.
Follow FTMA Australia for Industry News and Updates
Our Principal Partners


