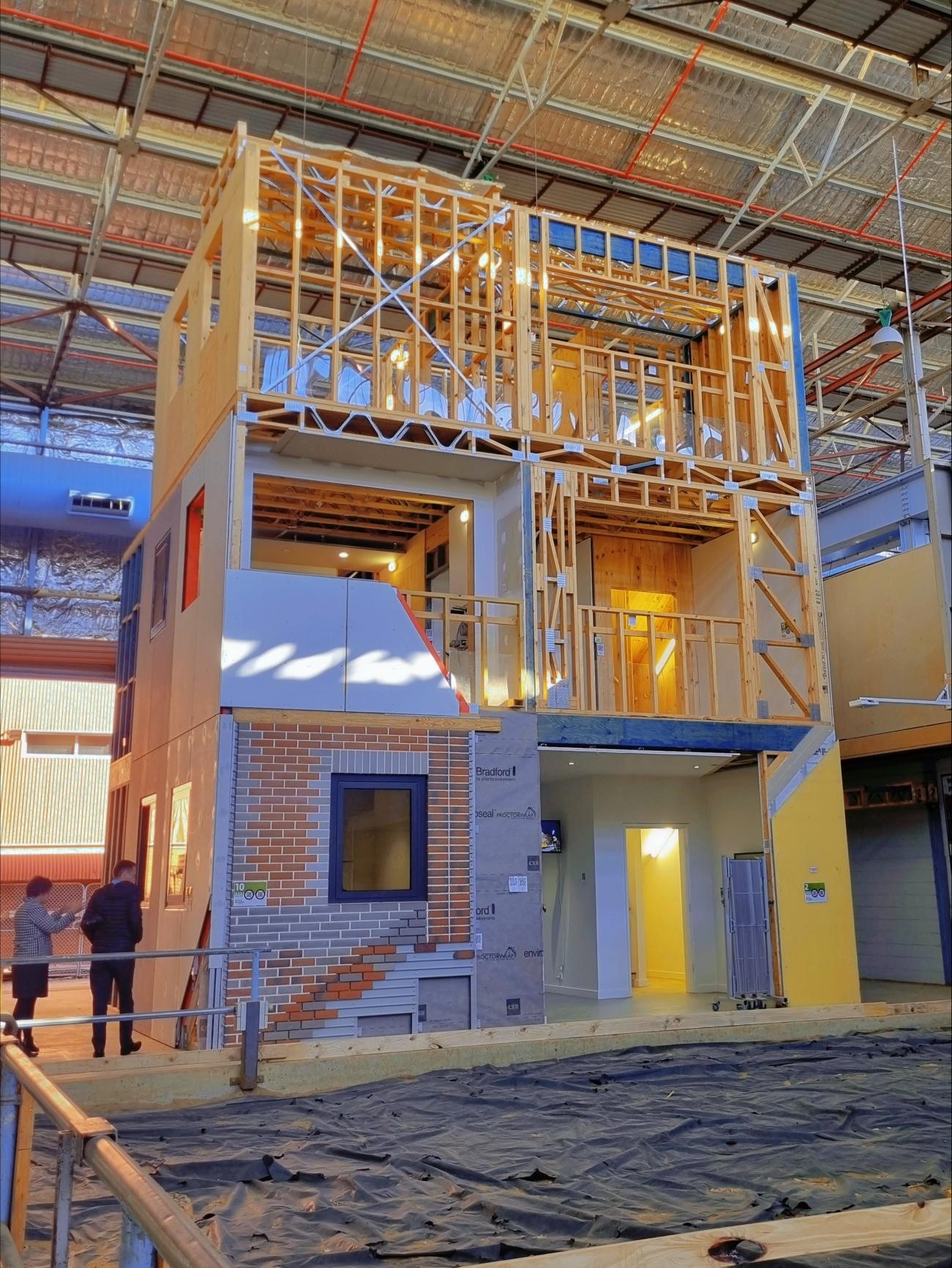
Written by FTMA’s Kat Welsh
At Holmesglen Institute’s Chadstone campus (Victoria), there is a remarkable example of design technology and educational resource – evidencing the possibilities, ingenuity, and future of Australian timber construction. In a corner of the Applied Building Technology space, sits the 3 storey Mid-rise Full-scale Demonstration Model (Mid-rise Model). The purpose-built educational model examples; lightweight and mass storey timber construction to suit different building classifications; how it is achieved with ‘behind the walls’ cut away features; and every element broken down into detail – making it a unique and valuable tool.
Back at the end of 2023, Australia made a promise. Representing our country, government leaders signed an agreement at COP28, stating:
‘Recognising that wood from sustainably managed forests provides climate solutions within the construction sector, we commit to by 2030, advancing policies and approaches that support a low carbon construction and increase the use of wood from sustainably managed forests in the built environment. Such policies and approaches will result in reduced GHG [greenhouse gas] emissions, and an increase in stored carbon.’ (From the Forest & Climate Leaders’ Partnership pledge.)
Australian government, under The National Housing Accord, has committed to building 1.2 million new homes across Australia over the next 5 years. The fly in the ointment might be that even at its most productive, the number of new houses built in Australia in one year currently stands at 124,500.
‘The data shows that system capacity to build houses is highly constrained at </=125,000 pa, while for the more flexible building mode of multi-res, the limit is probably untested but clearly capable of ‘flexing’ up and down as demand patterns change. This can be seen in the index chart below, where houses just cannot get moving.’ Tim Woods, Managing Director of IndustryEdge.
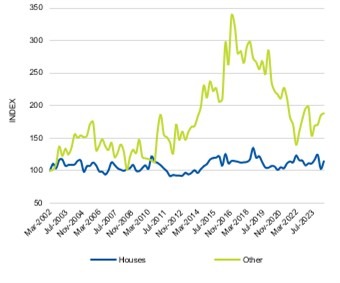
Image Credit: Industry Edge
While private enterprises hold the torch in Australia, when it comes to driving the environmental future of construction for the country, how can we en masse fulfill the housing targets government has committed to, with the requirements of living more sustainably? WoodSolutions and Holmesglen, might hold a key to this. What the Mid-rise Model represents is a way of building homes, as a solution to at least 2 of the biggest responsibilities our country faces.
Yes, sometimes you can kill two birds with one stone.
David Hulett, (Head of Department for the Applied Building Technology at Holmesglen Institute), and Dr. Alastair Woodard, (Wood Products Victoria / WoodSolutions), are dedicated to teaching the design methods of the Mid-rise Model, as a means of progression for the housing and building industry, whilst promoting the use of renewable materials.
The building is a collaboration between multiple program sponsors and supporters, directed by WoodSolutions. Following the changes in the Australian building codes (National Construction Codes) in 2016 and 2019, mid-rise timber construction became an allowable deemed to satisfy solution. The Mid-rise Model shows how a potential 7 storey timber mid-rise is constructed with engineered design systems. WoodSolutions have published a series of technical design guides that accompany the model – FTMA News have been featuring the guides each month in 2024.
‘The genesis of this came in 2016 when we were talking to builders about the code change and encouraging them to actually build these apartments, and the first thing they would say was ‘well show me one’. They were definitely around, but the problem is when you build them and encapsulate the timber, everything’s hidden. There’s only a short window when you can take them [a builder] to a site, and actually show them the timber systems you’re talking about,’ said Alastair.
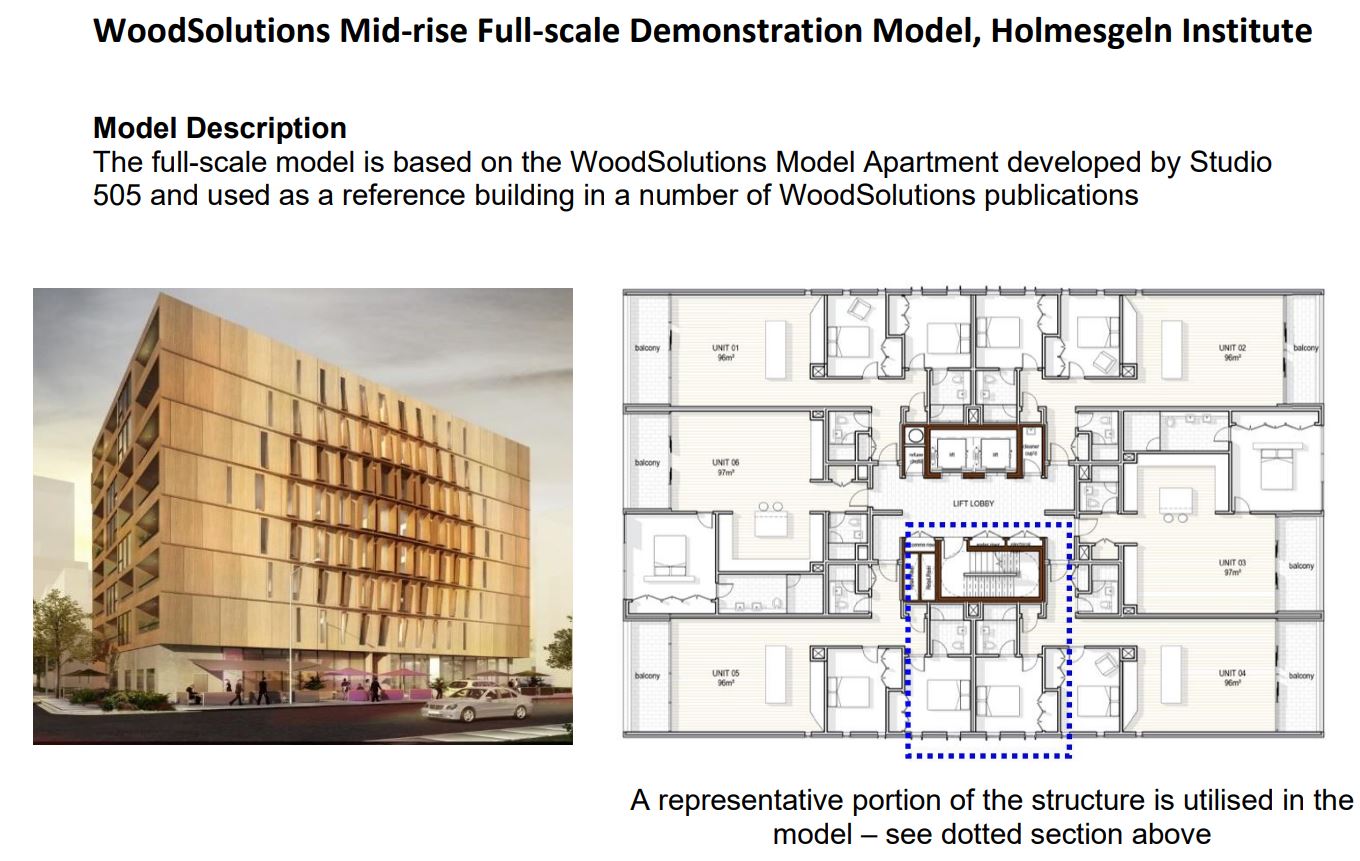
Australia’s definitely facing challenges when it comes to producing homes at the capacity the government have committed to, which means the way we’re currently doing things has to evolve.
‘We’ve got to start thinking a bit differently,’ said David, ‘with the shortage of product, the shortage of labour, they can’t keep on building the way that they are.’ Stick built framing onsite, can use up to 25% more timber than offsite prefab – even though timber is renewable, it must be utilised, not wasted. Offsite prefab assists building construction worker shortages, encapsulating as much as possible through factory fabrication, to reduce onsite labouring.
‘Using this building technology and methodology, reduces the amount of labour required onsite. If you’re shifting the responsibility of the development of the panels to someone else in a factory, and you’re managing the building and assembly onsite, that’s one way to manage your workforce,’ said David.
The Mid-rise Model determines many things – the abilities of building with timber, utilising offsite engineering, reducing resource wastage, decreasing build times, and providing quality homes. With the model’s unique construction, the cut aways show how all the design features work together to achieve the build. ‘It really is a system… it’s not just about the timber construction, if you don’t get the fire requirements right, the acoustics right, then the whole system breaks down. And if any of those elements break down, the timber will always be blamed… It’s really important for people to understand the elements of the system, and this allows us to show them exactly, how it needs to go together,’ said Alastair.
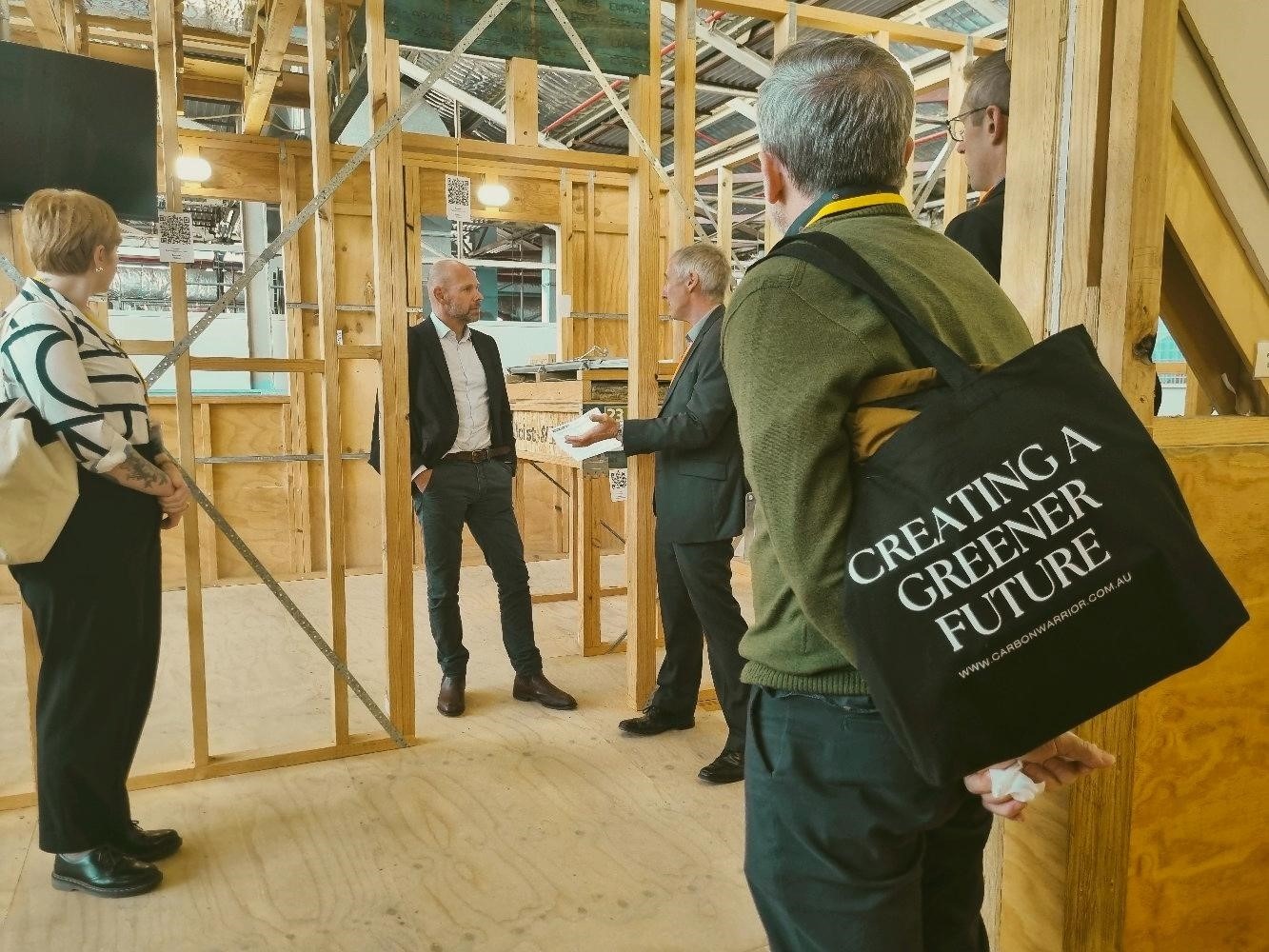
Witnessing the department in operation, Holmesglen seems like the ideal location for the model – planting the seed early with students banging in the background. This is the next generation of builders and carpenters, that could potentially be learning about timber design at the beginning of their career. ‘Alastair’s obviously trying to educate the industry, but we [Holmesglen] need to educate the people coming through first,’ said David.
A stumbling block at this point though, seems to be a lack of people practically knowing how to facilitate the install. It’s one thing to design and manufacture in the factory, another to get the experienced builder onsite to put them up. Also, the culture around apartment buildings in Australia has not left the ground, to the capacity it has in other countries. Something that David and Alastair want to change. ‘There’s been lots of quite tall, impressive office [Class 5] buildings made out of mass timber… there’s still huge potential for the Class 2 buildings,’ said Alastair, ‘it hasn’t really taken off as much as we thought it would. I reckon in Australia, timber probably has about 3 to 5% of this Class 2 market. In Canada they really hit that market hard. They converted the apartment market up to about 6 storeys, they’re at about 80% of timber at the moment.’
Recently, FTMA and WPV organised for Victorian government members to visit the Mid-rise Model. ‘If you invest in the social housing, you really should be offering the best construction you can provide that customer,’ said Alastair. He talked about the concepts behind Passivhaus, and also the design functions of the Mid-rise Model – building houses that require little to no heating or cooling, the impact that would have for people living in them, and the ongoing carbon footprint of the property. Potentially government could invest in the frame and truss sector, and the building designs from the Mid-rise Model – addressing environmental and housing targets, and the COP28 agreement, ‘If they’re looking to support certain sectors to develop, they need to be investing in the frame and truss sector,’ said Alastair, ‘we’re trying to find the companies that are keen to do that [the model], and help them do it.’
The Mid-rise Model exists for teaching purposes at both ends of the spectrum – new students, and for those already in the industry looking to advance. And FTMA is keen to assist this process, and expand the possibilities within the sector. ‘This model, is really an example of an apartment building, a Class 2 type building where someone lives above and below one another, so you’ve got to get all that fire and sound separation right. Whereas the frame and truss guys, the bulk of them, are in the detached Class 1, 1 and 2 storey market, and a growing number now supplying 3 storey townhouses,’ said Alastair.
The risks – in taking on larger commercial builds – are a reasonable concern for small businesses whose current expertise might be the residential sector. Where the design applications could be relevant to smaller frame and truss fabricators though, is townhouses. There are editions to the framing process that could be relatively easy to incorporate, to speed up processes onsite and increase builder productivity, without taking the bigger financial risk. Alastair talked about processes such as installing vapour barriers, window installations, external wall cladding battens, external cladding or full prefabricated wall systems (lined both sides), or provision of floor cassette systems (a highly productive solution for townhouse construction where repetition of units occur) – all increasing the products valuableness to the installation process.
For a virtual tour of the Mid-rise Model click below
Visits to the Mid-rise Model can be organised and are very welcomed, for fabricators, builders, architects, or others interested in finding out more about the design possibilities.
If you’d like to find out more or arrange a visit, please make contact with FTMA – let’s utilise this exceptional resource.
Our Principal Partners

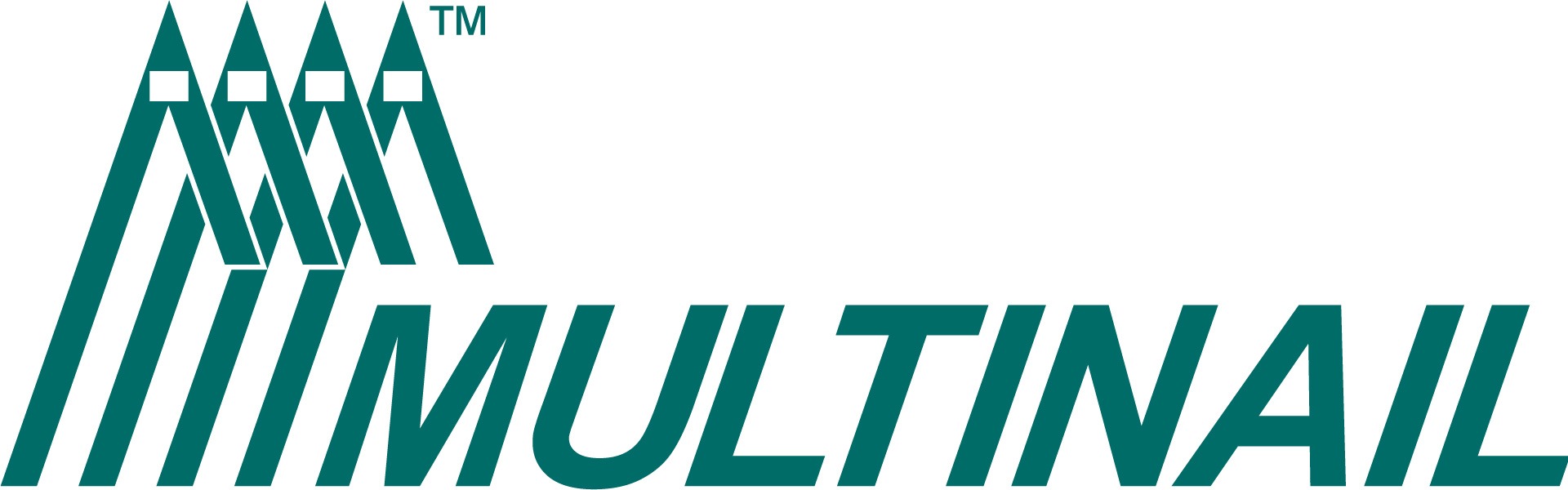
