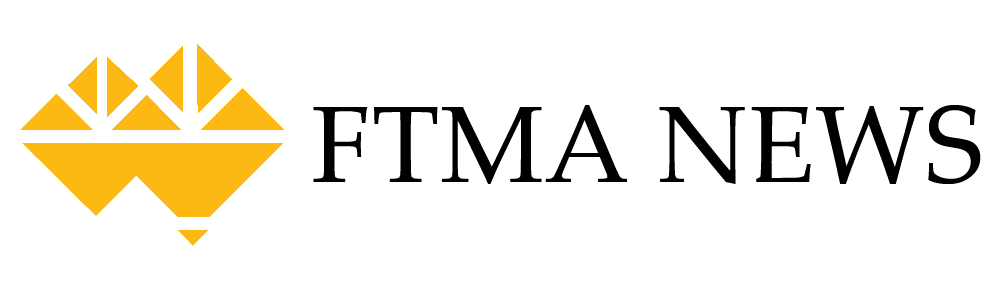

One of the earliest machines produced by Hans Hundegger AG in Germany was the SPEED-Cut. It immediately became a favourite in Europe amongst Carpenters and Joiners as the universal cutting and processing machine. As it developed, further options became available and its reputation grew as a true and trusted work-horse in the greater timber industry.
With the traditional strong travelling instinct of Antipodeans, the first “down-under” Hundegger customers discovered the Hundegger SPEED-Cut at the LIGNA Fair in Hanover, Germany. The robust and flexible 5-axis overhead saw aggregate on the SPEED-Cut was what first attracted the Australian and New Zealand market. These pioneering customers were generally from the Frame and Truss industry, and once these early machines were installed – many with the optional powerful Vertical End Mill for processing single or stacked double mitres, the game changed and the Hundegger SPEED-Cut became the heart of many Frame and Truss operations.

The Vertical End Mill was also an attractive option to timber importers and distributors as a machine that could be configured not for just 6-8m truss components, but 13m or longer for I-Joist feed stock. It could cut floor components with the required service openings on a job-by-job basis for the expanding mid-rise, multi-residential sector. Improving technology in printing directly on the components with ink-jet printers increased the flexibility and value of the SPEED-Cut even further. The SPEED-Cut became the linear saw of choice in Australia and across the Tasman. Further advancements such as the 3 head turret mill opened new doors for the SPEED-Cut in processing Glulam and other EWP.
However, one of the biggest advantages today of the Hundegger SPEED-Cut for the Frame and Truss industry, and one that “flies beneath the radar”, is the option on the SPEED-Cut to configure it with the built in Double Trenching Unit. Particularly in NSW, where trenching of top and bottom plates for stud location/fixing is common practice, the Double Trenching Unit built into the saw is a real game changer. Importing data directly with the job file, the SPEED-Cut can cut and then trench single or back to back plates with mirrored or individual trench locations. Where a single-width trench may be required on the top, but a double on the bottom, that is also possible when running top and bottom plates together.
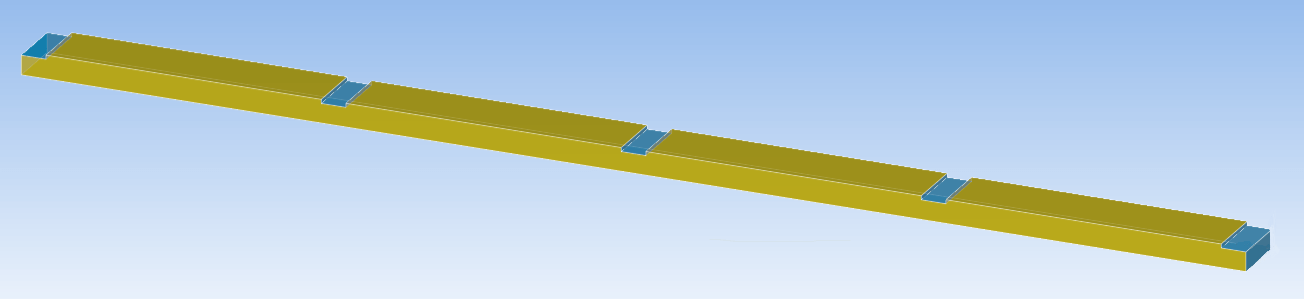

The Double Trenching Unit or the Vertical End Mill take up no more room on the SPEED-Cut footprint than when fitted as standard with just the 5-Axis Saw.
The tooling for the Double Trenching Unit is designed for you to suit 35mm or 45mm material, and it takes a single stroke to perform the required trench. Cutting depth adjustment is simple to allow the trench depth you desire, and it is then automatic regardless of whether you are running 35mm or 45mm plates or any other size.

The current process on a saw of cutting all the frame components, then separating out those that need trenching, ensuring the data on the trenching machine is correct, and reprocessing pieces on the trenching machine is time consuming and open to errors.
A long-time owner of a SPEED-Cut with the Double Trenching Unit says “our trenching attachment is great. Takes up no extra space, is fast, accurate and most importantly being part of the saw, all the information required on the plates for manufacturing and site assembly is printed on the plates as they are processed”. A further advantage with the Double Trenching Unit is that it means downstream assembly machinery can be less automated and costly to purchase or maintain. The assembly process is greatly simplified by the visual prompt of the trenched plate.
Sam Rowe, General Manager of Hundegger Australasia says that “increasingly, fabricators need to do more – with less. The Hundegger SPEED-Cut can handle up to 6m infeed and outfeed lengths (actually up to 13m lengths are available) and the total footprint is similar to most linear saws. Even including the Vertical End Mill and/or the Double Trenching Unit, it’s only around 60m2 of floor space.
Rowe says “The alternative is to have a standard linear saw taking up that same approximate 60m2, plus a separate mitre saw (about 22m2) and a separate trenching unit (another 16m2) and add in some space at each station for trolleys of work-in-progress material that has already been through the saw and you can easily lose another 60m2 or more of valuable space in a workshop. All of a sudden, you need 120m2 to accommodate all these separate processes. Plus, the material is handled many times more and the opportunity for mistakes increases.”
The Hundegger SPEED-Cut is fast, reliable and powerful. Easily the most flexible saw available in the region and a proven performer in the industry. “Over 80 SPEED-Cut machines in operation in the region demonstrates the pedigree” says Rowe, “and there are over 1000 SPEED-Cuts installed worldwide.”

Gold Sponsors


