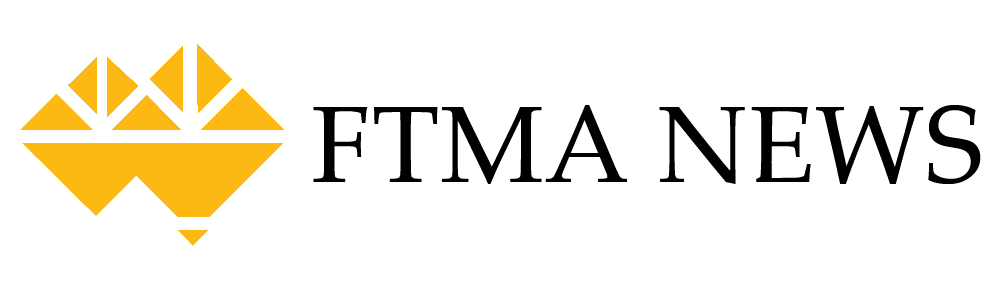

Dealing with reality – our opportunity for beneficial change.
As an industry over the past year or so we have had a roller coaster ride.
Clearly the 2 major factors that have occurred are bushfires and COVID response. Firstly and most enduringly is the impact of fire in the plantation estates. More so than anywhere else in the southern regions of NSW that houses large sawmills along with impacting other southern NSW and northern Victorian operations.
Not limited to, but representing the highest volumes are AKD in Tumut and Hyne in Tumbarumba. They and others have had to make serious and difficult decisions about how to handle a dramatic change in their circumstances that they had no control over. These operations over the years have invested considerable capital and thankfully they have done so as the whole industry has had the supply needed to run our businesses.
Their outputs over the past year have been supported by their contribution to recovering the usable fibre in burnt log. As this recovery process comes to an end they are now faced with the reality of the longer term.
The management and ownership of these mills are strong, proactive and resilient and have taken the steps to ensure a continued supply volume to the market. However, their log resource has and will change so will no doubt the recoveries. Although these mills do not represent the whole of domestic supply, their output is hugely influential and alternate supply is conditional.
Secondly, the government stimulus to minimise the economic impact of COVID has generated a ‘sugar hit’ in demand. It is really not known how much of this is new demand and how much is demand brought forward. Stalling of immigration is another major factor in what is a scale unknown in forward overall demand but is clear current activity levels won’t hold into the distant and maybe not mid-term.
To a certain degree the demand spike has been offset by the rush to process fire affected log. But even then, the demand has pushed supply.
For the fabrication sector to retain their market share, supply is required – no rocket science in that. Is there an available supply? Yes. Where should it come from? Australia. What would it look like? Different mix to what we’re used to.
Supply and price go hand in hand. Again not rocket science. But more pertinent, does a bidding war push up prices or do unit production costs rise in processing facilities due to the amortisation of cost over a restricted volume?
The long term threat is the latter. Higher prices with possible static or even shrinking volume. We as producers in our own areas know that fixed costs spread over high volume keeps unit price down. The finished fabricated product sold to the market has to be competitive. There is a ‘price point’ in what we sell. Go over the price point and the opposition moves in – usually for good.
We need our upstream producers to keep their unit cost within range so the whole supply chain can function. Essentially the mills have to keep producing high volumes. The cost to run modern sawmills is only going up so they are not in a position, financially or enduringly to spend less on their operations.
Given that the resource mix will change so will recoveries and grade yield. Now comes the time to think about what product we can expect of them and how we might need to adapt. This is where we take stock of what we have done as an industry up to now but far more importantly what we are going to do to adapt to a change in supply.
It’s not so much an opportunity but a necessity to change our habits for the better. Better utilise the resource that will underpin our future by maximising our basic raw material. That’s an absolute win.
Broadly & generally, the demand placed on mills by fabricators for the bulk of framing has been in the industry ‘standard’ structural grades of MGP10&12 and more often than not in long lengths of limited dimension. This is to feed linear saws that will optimise the infeed length into long chords as well all the other different component lengths that are needed for jobs. This is a fantastic way to minimise stock holdings and to circumvent the ongoing problem around adequate numbers of competent plant staff.
What has happened through this is the creation of a ‘one size fits all’ scenario in timber demand. The prospect that mills will be able to supply those vast quantities from a changing resource is not guaranteed. If demand specification remains that way it is pretty sure a constrained volume would be more expensive. This is because of both a bidding war and a higher unit cost due to overhead amortisation on tighter mill output. There goes the final product competitive price point.
Using MGP10&12 timber for long truss chords is right and good. Chord stiffness is necessary and the MGP grading process works well for that particular application. However these grades’ stiffness values are regularly and significantly over specified for other applications like webs, studs and anything short. When this ‘one size fits all’ approach is taken, way higher quality is used unnecessarily.
Mills have traditionally promoted grades based on stiffness in the past mainly due to production and market conveniences. It is not certain the concentration of grading primarily for bending stiffness as the critical design characteristic makes sense especially in a changing timber supply scenario and with better evaluation techniques.
A clear temptation, but certainly by no means the only option, is to establish an additional MGP8 grade or use more F5 where produced. Here is a left field idea – what about a C13 grade (Compression characteristic of 13MPa and with a suite of more appropriate other strength values)? Considerable volumes of timber that doesn’t achieve MGP10 bending stiffness threshold would still reach C13 and be perfectly suitable for many structural applications. Visual impact would not necessarily be compromised either.
Regardless or not if this type of approach is right, it is absolutely in the interest of the whole industry that a discussion is commenced on other ways to make the supply pie bigger. We are coming up to 30 years since the current MGP grades were introduced along with their assigned design characteristics. Whether or not we had to face the current market and supply conditions, it is time to at least review the options. An important fact is that these other options are priced very similarly to current MGP10 for the mills to see the required return on the basis of the potentially lesser log characteristic profile.
All mills, not only in Australia but globally have and continue to correctly work to ensure they find the better fibre in the logs they process and put it towards engineered and other high value products like glulam. The time is right to think about the lower end of the fibre range in the resource as well and ensure that once it doesn’t meet MGP avoid it being relegated to low value F5, packaging or even export but used to make truly fit-for-purpose products that increase availability, ensure application performance and keep the final fabricated product within the price point.
Over the past 20 years Programmed Timber Supplies has supplied the fabrication industry with fully fit-for-purpose components. We look forward to continuing to work even more closely with both suppliers and customers to ensure our Australian plantation resource is fully and responsibly utilised.


Gold Sponsors


