Is Steel Growing Its Share?
New Report for FWPA
A constant question in the forestry and wood products industries is to what extent steel house framing is growing its share of the Australian housing market. A new report, produced for FWPA, by Australian Construction Insights (HIA) addresses the question.
Before downloading the report itself, it is important to gain an understanding of the issues that impact decisions that inform supply and demand of house framing materials. Jim Houghton, FWPA’s Statistics and Economics Manager has prepared the following briefing:
There appears to be a significant macro challenge concerning supply (which I define as local production and imports). This will only become more difficult in the future as demand continues to grow.
So while we are talking about steel the realities are the supply and demand dynamics in the market will see substitute products emerge if traditional products such as timber struggle to meet demand.
As at Sep 2018 detached housing approvals are running at 120,000 units YoY and overall approvals are at 223,287 units.

If we look at that since 2000 we can see that detached homes – timber industry bread and butter has been relatively steady at 115-120,000 units. The big action has been in multi residential which at this stage is not strong territory for timber.
So why the issue with supply?
Where demand has increased for timber is in the town house development.
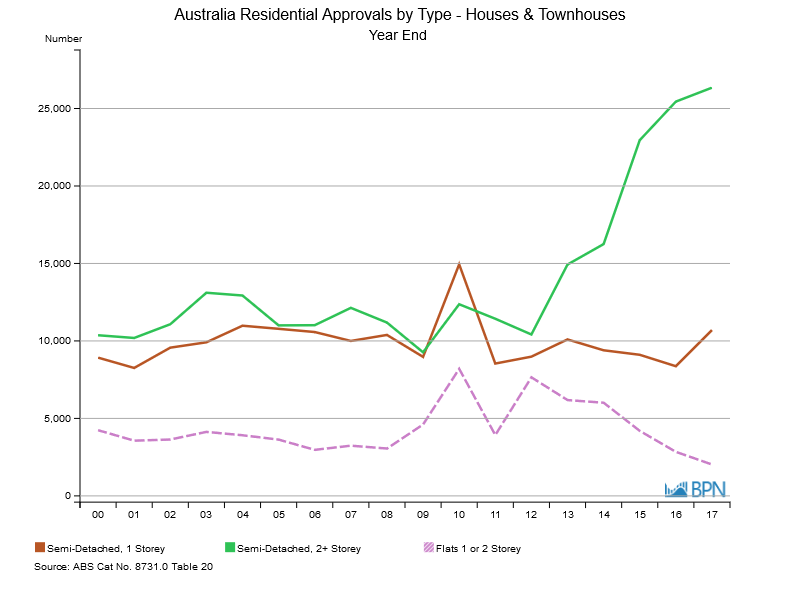
The big increase here is semi detached 2 storey+ which we know as town houses and which timber dominates. From the start of the period 10,367 units to 2018 M09 26,143 units YoY.
So with local production running at capacity the swing volume has been serviced by imports. This has always been the case and imports provide an important source of supply. The difference in the past 2 years has been the activity levels in North America and Europe which have now increased and been associated with improving prices. Refer to earlier article in this issue of Statistics Count
But this highlights the challenge that if local processing is operating at capacity then prices in other markets will influence the import volumes we can expect. Ie to say the swing volume will reflect more directly international parity pricing.
In the past 12 months that has required higher prices. That may change if the drop off in North America were to continue but the reality is higher prices are likely to continue.
ABARES in a report to be published shortly has modelled demand and supply through to 2050. Based on the current estate and other market factors the supply position will only become more challenging.

With continuing growth in demand for softwood sawlogs, ABARES estimates that this domestic log availability shortfall could increase to 3.4 million cubic metres per year between 2050 and 2054. To provide context to these figures an additional 200,000 to 250,000 hectares of new softwood plantations would be required by 2050 to meet an annual deficit of 3.4 million cubic metres per year (based on an assumed growth rate of 13.5 to 17.0 cubic metres of sawlogs per hectare).
Constrained supply and associated higher prices (the markets logical response) will create opportunities for substitute products. So it is important to note that any tactical responses to substitute products needs to be considered in the context of the supply and demand outlook.
Steel Framing
Against that background what do we know about steel framing.
The report prepared by ACI/HIA Framing Material use in Residential Construction has surveyed builders in Victoria, NSW and Queensland to determine framing material use in 2017-18 period. The report also analyses factors affecting builders material purchasing decisions. The full detail of the report can be found on the FWPA website.
The key finding for the detached homes is:

The Victorian Building Authority data has been mentioned in the ACI/HIA report and is quite a useful data set – for Victoria.
That shows a 1.0% change in steel framing usage over the period.


However that detailed data is not available for other jurisdictions.
A broader approach can be seen in generic market research. FWPA recently purchased a study by Transparency International – Steel Framing Market July 2018
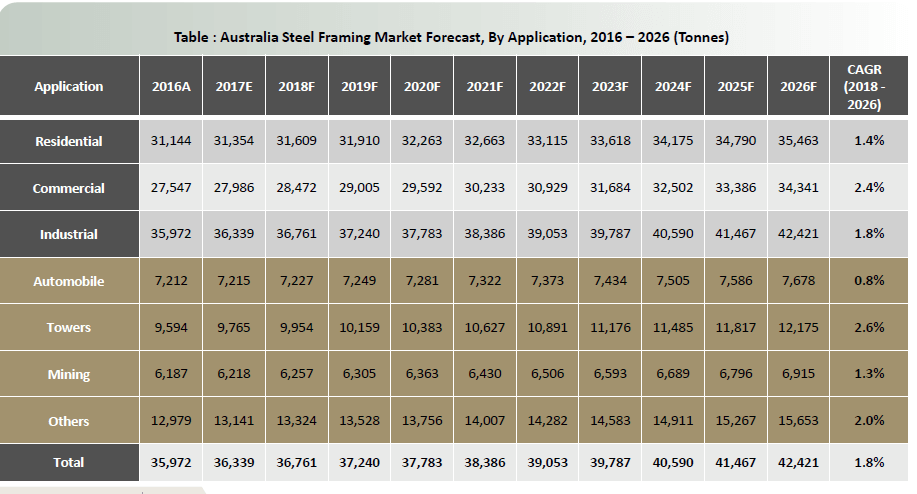
So the key here is what does 31,144 tonnes of steel framing feedstock represent? Based on a simple analysis of the lineal meters of timber framing in a detached residential house and applying the following kgs per lineal metres the following assessment has been made:

In the context of the VBA data this is probably about right.
The Building System
Comment made during the workshop indicated that an installed solution was something builders were looking for. This would involve greater modular construction with off-site manufacture of wall frame and roof trusses right through to on-site installation.
FWPA is currently undertaking an anecdotal survey of builders to better understand purchasing decisions builders go through in selecting the type of raw material used in residential roof trusses and wall frames.
Challenges in understanding the building system have also been raised in some recent work by Dr Eshan Gharie, RMIT looking at housing starts and completion rates. This work identified that on average we are only completing the same number of detached homes but are taking longer to build them.
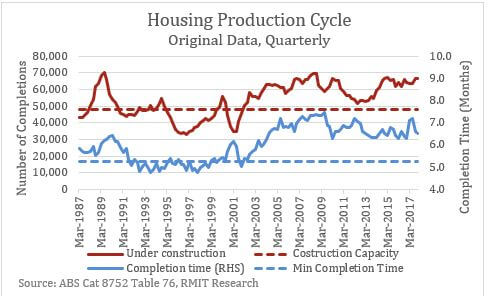
The work suggests there is a clear correlation between the number of houses under construction and house completion time. This strongly suggests that the housing sector works like a production system. When the number of houses under construction (WIP) rises beyond a “steady state” level of capacity, average house completion times increased. Or another way of looking at this is as demand (houses under construction) increases beyond current capacity the same number of houses are being built (completed) but it is taking more time to do it.
Or another way of looking at this is if you put more work into the system (houses under construction) in circumstances where the sector is operating at capacity then you will only get the same number of units out the other end (housing completions). However, what has changed is the time taken to build (completion time) is longer. This is a big challenge as the longer completion time will usually be associated with higher costs – the old analogy time is money.
Dr Gharie’s analysis suggests that the break point for houses under construction falls on 48,000 houses. Beyond this level the completion time increases and whenever the number of houses under construction is below this figure the completion time is at its minimum levels. That minimum level appears to be 5.25 months (1.75 qtrs)
Further work is therefore needed to better understand the Building System and in particular the value proposition for timber.
The ACI/HIA report for FWPA – Framing Material Use in Residential Construction can be downloaded here.
This article was written by Jim Houghton for FWPA’s latest StatisticsCount.