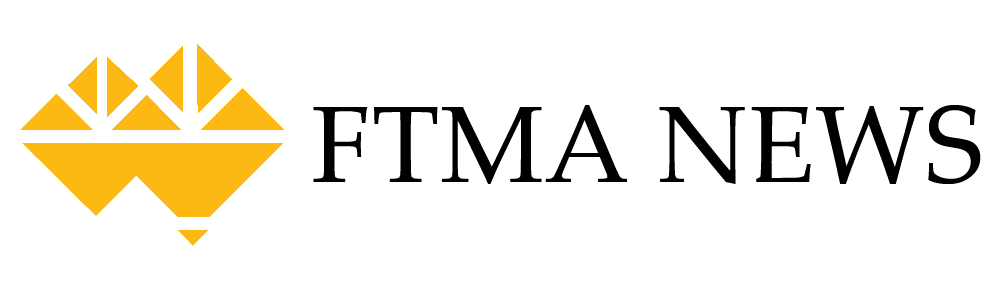

Regret – a negative cognitive or emotional state that involves blaming ourselves for a bad outcome, feeling a sense of loss or sorrow at what might have been, or wishing we had made a different decision in the past. Regret originates in a comparison between outcomes of a chosen option and the non-chosen alternatives in which the latter outperforms the former.
Regret sits on a scale from the simple everyday regret- ‘I should have stuck to the speed limit’ or ‘I should have brought the washing in before the rain’. Then there are the regrets that keep you awake at night- loved ones, family, friends, the person who got away or the words you didn’t say. No matter what causes the regret or where it sits on the scale, the emotional response is the same- sadness, remorse or disappointment.
At Vekta, it is interesting how many times we hear about regret from our customers.
‘… The only regret I have is that I didn’t buy it a couple of years sooner.’ Bruce Wallace, The Truss Joint
‘Just hurry up and do it, I wish I’d done it 4 years ago!’ Dean Kidd, Kidd Truss.
‘… I reflect on what we had to put up with over all the years before the purchase of our Vekta Razer S5. We wonder how we got this far without it…’ Alan Donagal, Timber Walls and Trusses
So, what is it exactly that creates the regrets for Vekta customers? Why would not purchasing a Vekta Razer sooner create a regret? To better understand this – it’s only right to hear directly from the customers!
Expectations
Regrets often revolve around expectations. The reality does not live up to the expectations created in your mind – consider TV-shows, movies, restaurants, online shopping experiences. For the Truss Joint, the expectations for their Razer Saw were exceeded.
It’s meeting all our expectations, I am sure there are others that use it differently, but generally we get timber in, timber out and it’s labelled and cut exactly how we want it. It’s the best piece of machinery that I’ve put in. I mean the other saw that I had when it went in… was the best bits of machinery you could buy at the time, you wouldn’t go back to one of them, that’s our recut machine and it probably will because with the Razer, it’s going, it’s flying along!
For Richard Schoof at Rainbow Frame and Truss in Albany, WA it was the speed of the saw that exceeded expectations.
The speed of operation compared to the Mango saw immediately improved, what we used to cut in a day, the Razer will do in a couple of hours. Also our use of timber has improved. We used to carry a lot more stock and different lengths. You’d have to work it all out in your brain, now the saw does it all for you. We’ve really been able to reduce the amount of stock held.
For Dean Kidd at Kidd Truss there were a few surprise elements that exceeded expectations.
There are two features that have really stood out for me. The ability to run ‘Razer View’ on my computer. I can sit in the office and oversee what is happening in production, review statistics and if the guys get stuck I’m instantly notified and able to help. The ‘on-the-fly’ cutting (optimising random lengths of timber) is also fantastic. I’m able to put re-used timbers on the live deck and the Razer automatically works out what can be cut using them.
Andrew Sternberg from Dahlsens commented:
The Operators especially love the printer (Vekta P3 Printer). The ability to print the plate location on the truss chords provides a huge advantage when putting the trusses together. For management, the feedback loop is fantastic. The ability to see what timbers are going through the saw, and the down and uptime allows us to review internal processes and make the improvements necessary. I also appreciate the ability to make changes on the fly and test them before going live.
Alan Donagal from Timber Walls and Trusses:
A few years in and the benefits have exceeded our expectations. Not only from a financial point of view in a number of areas, but we have also ‘deskilled’ our plant as far as requirements for employing workers to cut truss components. Also, the safety aspects in the use of cutting equipment is now not an issue.
Future Considerations
Regret often happens when a decision is made then something in the future (controlled or not) changes resulting in the earlier decision being regrettable. Booking that European summer getaway for July 2020- regrettable decision. In relation to automated machinery for the Frame and Truss industry- capacity is not something you want to regret.
We’ve grown over 50% in the last 2 years, the saw has had a big part to play in that, from a cutting point of view, knowing we could do that and having heaps of capacity up our sleeve, we know that’s not an issue for us… We are still only running at 60-70% capacity at 60-70% speed when we are cutting at that high end of what we need to produce. So we’ve still got a lot of capacity left in that saw and from where I sit I don’t have to worry about sawing capacity for some time now which is really good and I know when I was at another company and there was a lot of growth we grew quite rapidly over a period of time, sawing you know, we’d fix something and we’d be back at the saw for our bottleneck, so you are always upgrading your saw. Knowing there is so much more capacity left on that saw is very comforting.
Bruce Wallace – The Truss Joint

In Ballarat we’ve been able to reduce our wastage by 60% thanks to the Razer Saw. We also get an extra 30% efficiency in cutting in the same period of time than from other equipment.
Andrew Sternberg, Dahlsens
I was interested in the Vekta Razer as my prior history with the Razers had been good. I wanted something that was proven in the market and could be trusted- if something breaks down I need it fixed and I felt that Vekta and the Razer gave me that assurance. The footprint was also important- it needed to fit into my factory space… One of the main benefits was dealing with an Australian supplier and support team.
Dean Kidd, Kidd Truss
When it comes to automated machinery, the support you receive is definitely not something you want to be kicking yourself over! So, what do Vekta customers say?
Vekta service is something we can’t fault at all. We’ve probably only had the saw out for a day maximum, maybe two. I remember in the early days, Ed would be in America and he would jump on his phone and log in and correct any issue. Being located in a remote area the support was a big concern. It’s different for the big companies with two or three saws. If one goes down, they can still keep operating but when you’ve only got the one support is more critical. If it breaks down we need it up and running quick and smart. I really can’t fault the Vekta service and support at all.
Richard Schoof – Rainbow Frame & Truss
Ross Wallace at The Truss Joint commented:

Vekta support is pretty quick! Yeah, a couple of times I put the ticket in, normally within half an hour someone’s onto it. It’s good and sometimes I haven’t got all the info ready. You know it’s the same as anywhere else you have turnover of staff and you are bringing new people in and training them but I think from a training point of view when we are talking with people they are not going ‘I don’t know I will have to find out’ they are generally well trained and versed in what we want and being able to fix or get someone to fix it for us quickly. I put a ticket in early one morning, we wanted to put our logo on and be able to print it on the bottom chords so it could be seen. The guy from New Zealand rang in no time, I went out and logged him on and bang, bang, bang, next thing you know it was on there.
Nathan Salama, Sydney Frame and Truss:
When issues tend to arise, the new system allows us to quickly alert the team to have things resolved rapidly. This form of interaction is especially useful as it creates less down time. After a brief phone call, a technician remotely logs into the machine to rectify the issue. This process has been great, the technicians have been extremely helpful in answering questions on product knowledge and resolving our issues in a timely manner.
Dean Kidd, Kidd Truss:
My operators have all had experience with different linear saws. They really love the Razer and how easy it is to use. They’re enjoying having no overtime. The installation was perfect, completed over two days and training started on the third. The whole Vekta team has been fantastic! David was awesome, he was helpful with the guys and took his time with helping them learn.
Andrew Sternberg, Dahlsens:
The support and service is second to none. With Vekta we can get constant support. We can call any time of the day and do not need to worry about time zones. We can ask the stupidest questions and get a response within 24 hours. It has been a struggle to get information from other countries. We can also get spares and consumables delivered within 24 to 48 hours.
As emotional people we are always going to have regrets. The emotion of wishing we had made a different decision in the past will always creep up on us. Living a life with ‘no regrets’ is just a catchphrase. If you can learn from the mistakes others in the industry have made it is this – contact Vekta and find out more about our automated equipment for your Frame and Truss plant. From Razer Linear saws, PackFeeders, Truss Transfers, Smart Conveyor Lines and StakPros to name a few.
You won’t regret it! info@vekta.com.au

Gold Sponsors


