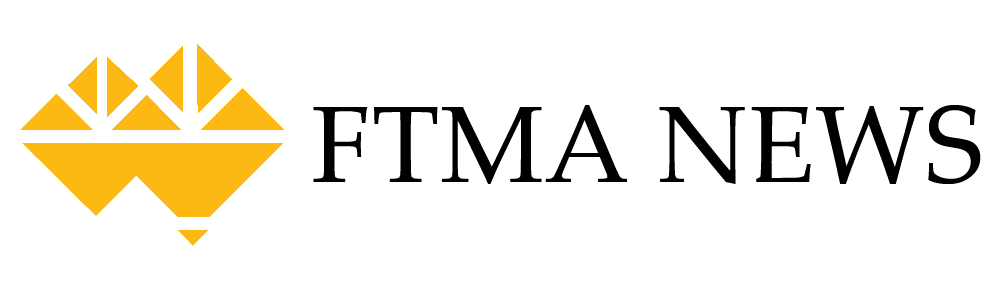

If there is one thing that COVID 19 has taught us it is that nothing stays the same. FTMA recently brought this to our attention, referring us to the ‘Who Moved My Cheese’ book.
This book has some excellent lessons to help us cope with the past few months, the coming months and life in general.
What works today, won’t necessarily work tomorrow. As the environment changes, our businesses may benefit from change too – or we risk being left behind.
Even when things look good, it’s good to keep an eye out for new, exciting opportunities.
Converging trends in our industry – manufacturing post COVID
The aligning trend of two distinct industry drivers has been becoming more obvious to Programmed Timber Supplies over time. Neither trend is individually remarkable but combined they held opportunity that warranted a further capital commitment by the company.
The first trend is in line with virtually all manufacturing globally, where skills and product complexity is being driven back up the supply chain. Economy of scale can be more easily achieved where a sensible level of processing centralisation is employed. The further down the supply chain, the more concentration there is on assembly as opposed to manufacture. This is happening in the domestic timber supply chain and with good reason.
The increasing demand PTS sees for pre-cut components clearly supports this trend. Also, not surprisingly, every other industry globally is moving in this direction for a number of reasons and most notably with competitive industry, skills and operations are moving up the supply chain. It is just like builders seeing the advantage in buying in their frames and trusses pre-fabricated because they either don’t want to or can’t get the skills on site. This is not to mention the greater economy of scale gained by ‘compiling’ manufacture.
Post COVID it is expected that automation and outsourcing will be key components of both the effort to revive manufacturing in many countries, but also to future proof existing domestic manufacturing. Trends also include on-shoring or near-shoring to prevent supply chain disruptions for many companies.
“While previous off-shoring trends were fuelled by a race to the bottom in terms of labour and productivity costs, advances in automation and robotics have drastically increased productivity across a number of manufacturing processes. Many of these processes can be easily re-shored and deployed domestically. Automated manufacturing will not bring back demand for low-skilled labour, but will create new jobs and opportunities for digitally-savvy workers”.¹
Another consideration for companies of all sizes, and across all industries, is that outsourced manufacturing or component supply works best when there is a level of visibility and the ability to share forecasts, orders, and inventory across partners in the entire supply chain. With this visibility, companies can ensure continuity of supply, jointly resolve disruptions when problems occur, and gain access to expanded revenue opportunities. Improved visibility also enables a host of opportunities for process improvement and cost reduction.
We digress, but the puzzling thing is that FLGM (Folder Light Gauge Metal – otherwise known as steel framing) promoters are trying to convince an industry to go the other way. By having to fold flat light gauge metal before it can be used effectively makes fabricators/manufacturers become ‘Processors’. Thus incurring more steps in the process before finished goods can be invoiced. More cost, more risk, more labour, more quality assurance and more overhead. It is a difficult proposition to have suppliers expect their customers to do more work before being able to raise an invoice and one that generally bucks the worldwide trend.
The second driver is the domestic need to achieve better utilisation from our forest resources. Last summer’s fires have only exacerbated this situation but it was clearly apparent before then. With Australia already being a nett importer of forest products and with per capita timber demand increasing, the pressure for optimal local fibre utilisation is essential.
The PTS business model neatly, clearly and succinctly addresses these drivers. More fit-for-purpose products to optimise available domestic wood fibre. PTS has clearly demonstrated that absolutely suitable components can be sourced from that part of the plantation resource that doesn’t achieve long length structural boards or high characteristic value fibre.

What have we done at Programmed during COVID?
Addressing these drivers combined with twenty years of experience gaining knowledge of the individual market sectors, specific customer needs, product development and performance with regional wood fibre characteristic understanding, provided the confidence for PTS to expand capacity.
When the scanning technology was introduced, consideration was given to future demand and allowance for such was made in the original equipment specification. At this very time the commissioning of another high speed saw is occurring. This will almost double the capacity of that scanning line.
The expansion of the PTS processing capacity stands to be of a benefit throughout the entire supply chain. Ultimately it returns better value back up the supply chain through extracting as much value as possible allowing better economic return whilst also offering customers a processed product that is convenient and cost effective via a processing economy of scale.
This video is file footage of a saw the same as our saw at Programmed Timber Supplies but a slightly earlier model.


Sources:
What will Manufacturing’s New Normal be after COVID 19 – Industry Week, Technology and IIOT1
Outsourcing Manufacturing: A 20/20 view – e2open
Trends and Traps in Supply Chain Outsourcing – Logistics Bureau
Gold Sponsors


