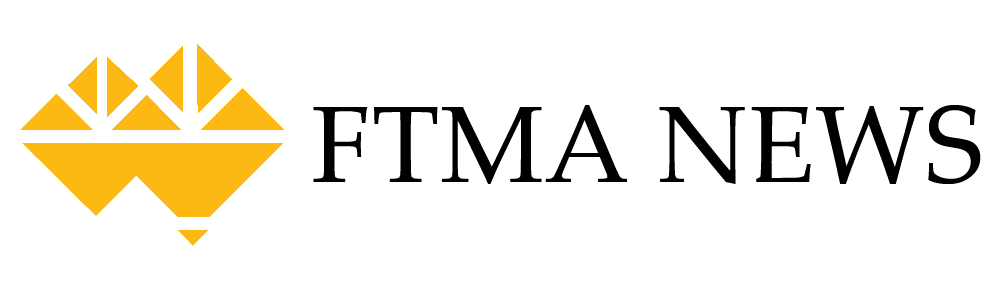

In 2017 I had the experience of going to Northern USA and Canada on a Wood Solutions Tour. The one thing I was particularly interested in seeing was how light weight timber-framed construction was incorporated into taller timber buildings.
We saw example after example of timber stud frames and I-joists being used to build apartments and hotels between 3 and 6 storeys high. Most would incorporate a first floor concrete transfer slab before the upper floors were constructed on site. The cost savings for the builder mean these solutions are accepted and commonplace.
So, what are the challenges to making the provision of light weight frames and floors for Tall Timber Buildings standard practice in Australia? How do tall timber buildings in light weight framing compare with a typical residential building? Well, at the core not much changes.
As a colleague likes to say when asked how to build a four storey timber building, “How do you build a four storey timber building? Well… you build a two storey house and stick another on top”.
I like to say, Tall Timber Buildings have two main problems. They are too heavy and too light at the same time.
If we compare the weight of a tall timber building to a house, it is a lot heavier. The building is heavier than a regular house as each floor has additional mass of material for acoustic and fire protection, as well as the fact that we have more floors. The walls must be stronger too hold up the heavy building and we have to consider how much the building is going to settle over each floor.
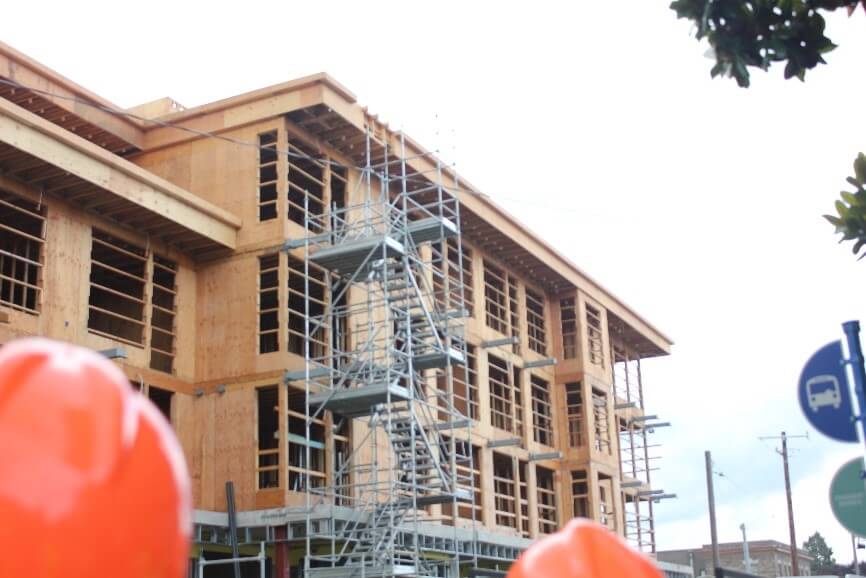
Figure 1: Typical 3 level timber-framed over 1 level concrete slab in USA
The solution is simple. The walls may become slightly thicker, and we may use materials that take load slightly better, such as LVL wall frames. Phoenix Apartments was built using a lightweight timber framing solution with LVL wall studs and plates.
Due to the weight of the building and the number of floors, we expect these buildings to shrink over time. For Phoenix Apartments the walls on each level were predicted to settle during service life by about 6 mm. Phoenix Apartments has been monitored since completion. So far, we have seen about half the predicted movement occur on site.
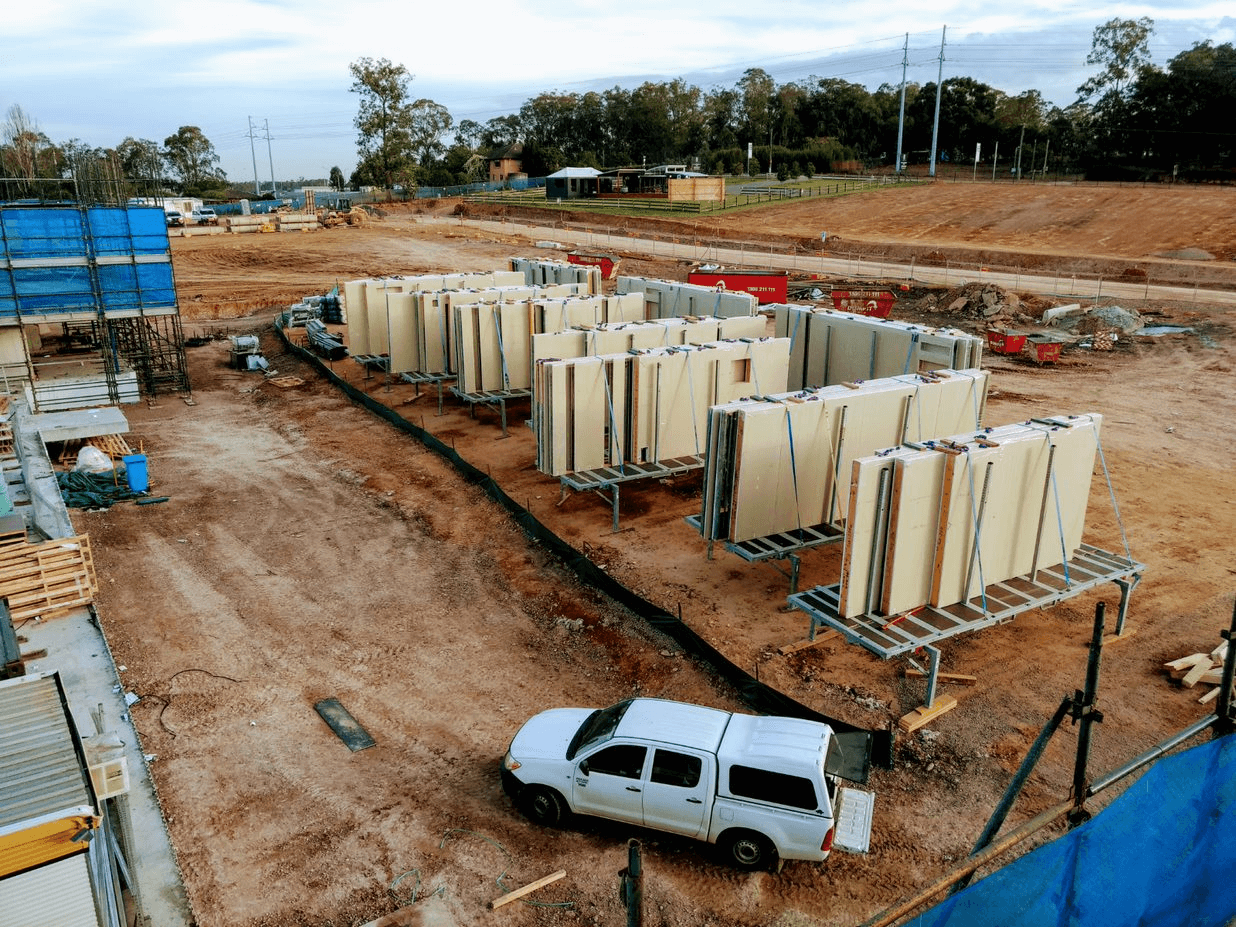



Figure 2: Offsite manufactured and clad timber wall frames using LVL studs for Phoenix Apartments
At the same time if we compare the weight of the building with a concrete building it is very light and is more susceptible to the effects of wind loads. Compared to a concrete and masonry build the building is considerably lighter, that means the footings save the builder money. On the other hand, we have to design for the building being lighter and easier to blow over.
To deal with the fact that the building wants to roll over we need to allow for tiedown rods (or overturning rods). As well as having the capacity to take the rollover loads due to the building being light weight, the rods must also account for the fact the building is heavy and shrinking by 6-8 mm per floor. The good news is that there are many systems that meet these requirements already available on the market.
For the Frame and Truss plant the changes required do not greatly change the process. The biggest challenge perhaps is the process. These building have lots of floors and walls, but only one roof. This means the mix of products through the factory changes. The challenges are large but so are the opportunities.
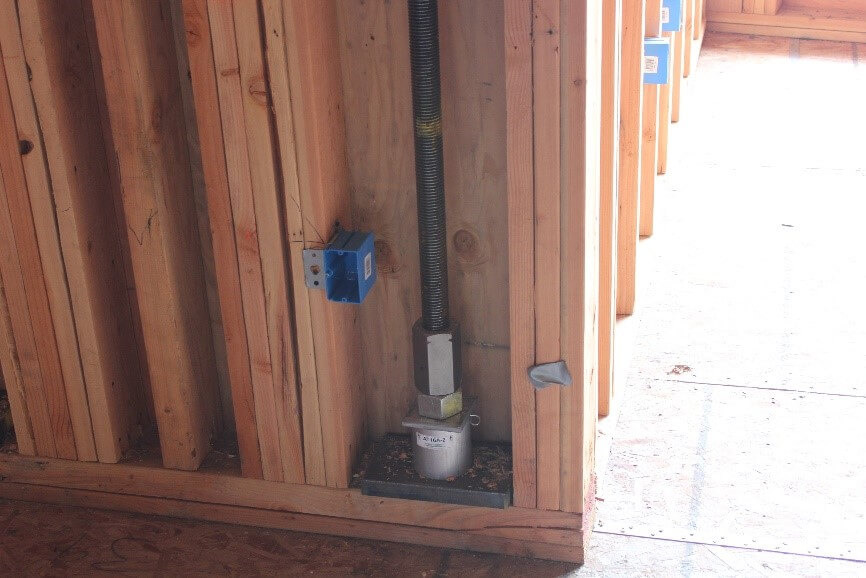
Figure 3: Overturning rod with Compensator to keep the rod tight as the building settles.
About the Author:
Stephen Dayus started his career in a small-town consultancy before joining Multinail and working as a Senior engineer. After a brief time managing a small truss plant Stephen joined Wesbeam where he is currently the Technical Manager, looking after Wesbeam’s team of Engineer’s and Floor Detailers. Stephen is passionate about the future opportunities for timber-framed solutions within the whole construction industry.
For further information about Wesbeam’s activities please see the Case Studies at www.wesbeam.com