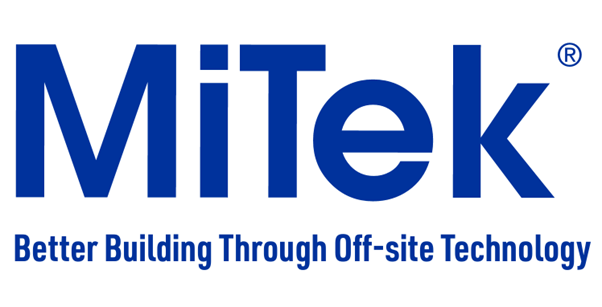
This piece was written and provided by FTMA Principal Partner, MiTek.
In today’s challenging market, marked by labour shortages, rising costs, and compliance complexities, the need for innovative building solutions has never been more pressing. At MiTek, we take pride in our collaboration with our fabrication partners to pioneer better methods of construction.
Let’s talk about a better way to build.
We continually assess the trajectory of the housing market and its implications for our fabricators and building partners, both now and in the future. Recognising the necessity to do more with less to overcome market challenges and we are constantly exploring different approaches.
MiTek advocates a unique approach to building, epitomised by our collaborative Design-Make-Build® process. This off-site construction methodology integrates efficient off-site construction methods into the concept and design phase, focusing on three key stages: Design, Make and Build, to achieve superior build outcomes.
MiTek’s Tim Rossiter highlights the advantages of our approach, emphasising the benefits at each stage facilitated by off-site technologies. “Our software enables us to design structures that are not only easier to make but also simpler to build. When we design, we prioritise understanding how they will be made and used throughout the build process, facilitating seamless collaboration across all stages,” explains Tim Rossiter, MiTek General Manager, Building Solutions. “We are actively collaborating with our customers to provide better solutions,” adds Rossiter. “Optimising the build in terms of time, cost and labour efficiency is a significant focus of our mission.”
MiTek recently put our methods to the test with a comparative side-by-side build in Queensland. Collaborating with Innovative Design and Build Group, along with our fabrication partner, we constructed two identical builds using different methods: one utilising I-Joist and materials assembled on-site, and the other employing The Posi-Strut Flooring system – Including No Floor Hangers (NFH). Precise cost and timing data were meticulously captured, with trades providing unbiased feedback.
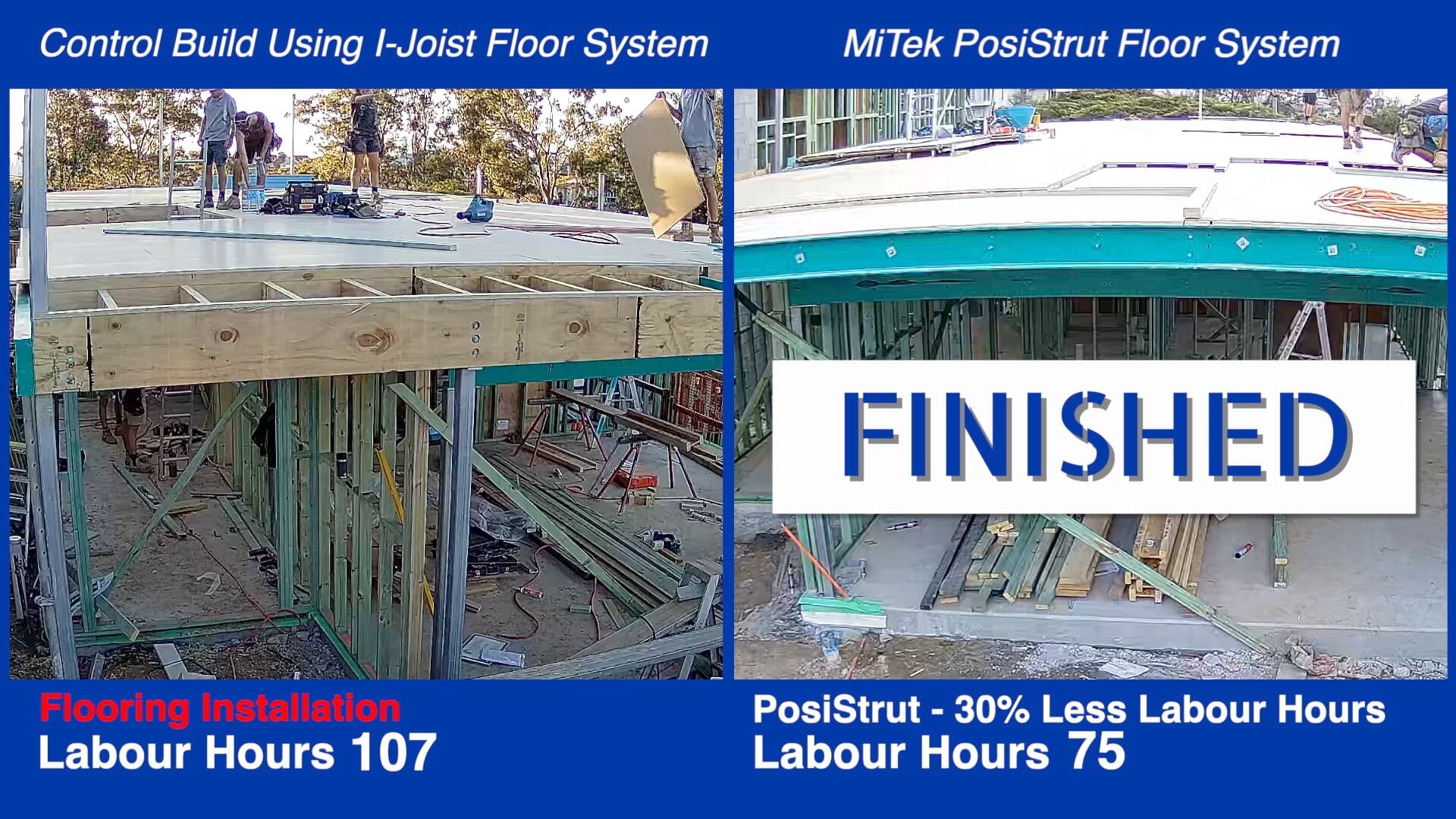
The results were compelling: The Posi-Strut floor system emerged as 2% cheaper than I-Joist when considering all of the material costs alone. Notably, labour costs were 65% lower for the Posi-Strut project, resulting in a completed build that was 10% less expensive. From a time-efficiency perspective, the Posi-Strut project achieved a significant time saving of 5 days, representing a 30% difference, unlocking numerous opportunities for our customers to enhance productivity and profitability.
Beyond cost and time savings, the Posi-Strut system offers a myriad of value-added benefits, including waste reduction, streamlined processes, reduced risk factors and enhanced sustainability through precision production. Additionally, the streamlined construction process facilitates faster project completion, improving cash flow for builders and increasing capacity to take on additional work.
Trades involved in the project praised the ease and confidence afforded by the Posi-Strut system, highlighting its potential to diversify and expand the labour force within the construction industry. By prioritising efficiency, quality and innovation, MiTek’s Design-Make-Build approach underscores our commitment to sustainable, cost-effective and future-proof construction practices.
As we continue to collaborate with our fabrication partners, we remain committed to innovation and providing better outcomes for our customers. With its proven efficiency, affordability and enhanced performance, the MiTek Posi-Strut floor system emerges as a compelling choice for modern construction projects, paving the way for a more sustainable and resilient built environment. Let’s continue to explore a better way to build, together.
Our Principal Partners

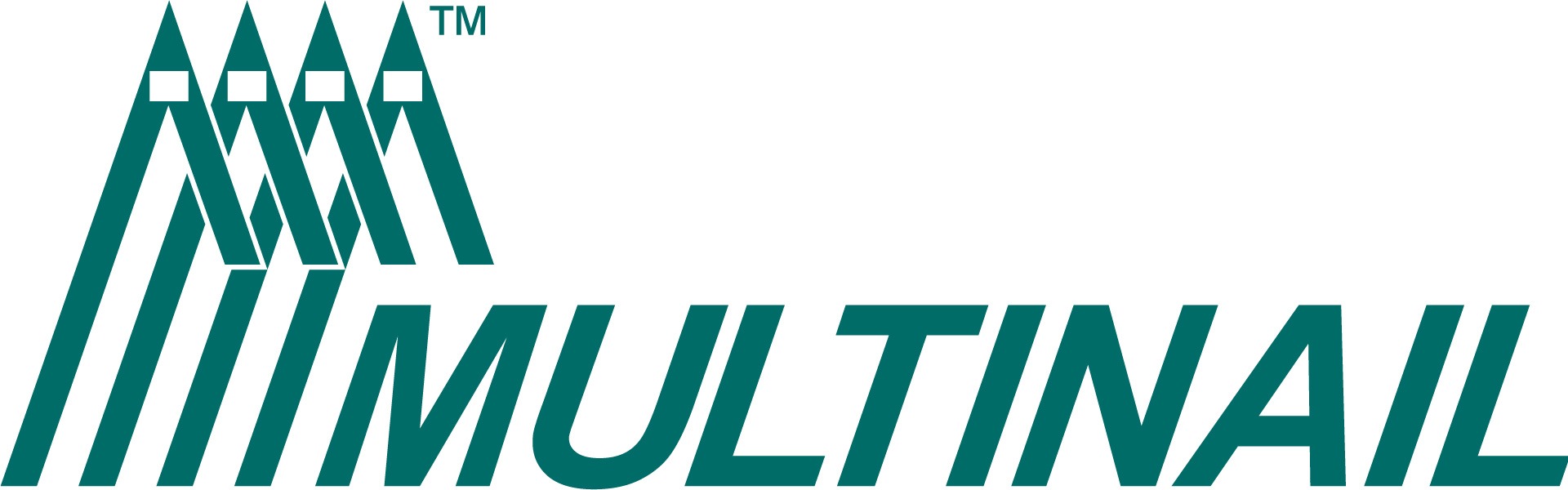
