There is a rapidly increasing level of interest by the building community in Australia, and around the world, in designing and constructing mid-rise timber buildings for apartments, hotels, offices, aged care facilities and schools. This has come about both due to:
- changes in the National Construction Code (NCC) back in 2016 and again in 2019 that now allows under the Deemed-to-Satisfy (DtS) provisions the use of ‘fire protected timber’ elements (timber encapsulated with fire-rated linings), if the building also includes automatic fire sprinklers, cavity barriers and is under an effective height of 25m – approx. eight storeys, and also
- the growing interest by building professionals in using more environmentally friendly building materials.
This now provides a huge new market growth opportunity for timber construction and fit-out products outside the traditional residential home market. The cost-efficiency benefits of these type of projects is strongly influenced by the increased utilisation of offsite prefabricated timber systems that rapidly speed up the onsite assembly times, and this is where a unique opportunity is opening up for innovative frame and truss fabricator companies.
Offsite prefabricated timber systems of greatest demand in these new mid-rise projects include lightweight floor cassette systems – around 3.0m wide and lengths up to 12m, partially enclosed or fully-enclosed wall systems, braced lightweight shafts, and trussed roof systems.
To assist the frame and truss sector in developing the technical expertise to tackle this new mid-rise timber construction market a collective and collaborative group initiative has been running for the past two years. Known as the Mid-rise F&T Market Implementation Group, or the MIG for short, this group facilitated by FTMA and Wood Products Victoria meets every two months and brings together the technical and marketing staff from the three nailplate companies as well as over a dozen F&T fabricators nationally, interested in mid-rise timber buildings; the group also includes representatives from EWPAA, ATIF and the WoodSolutions Mid-rise Advisory Program (MAP) team.
The first phase of the MIG program focussed mainly on the technical questions, and design and assembly processes of taking lightweight timber framing, from the commonly accepted three storey level, to four – five – or six storeys high. After some excellent collaborative work, the technical staff of the three nailplate companies all are now able and competent to advise and assist any of their F&T fabricator members who might be interested in exploring these new market opportunities. If this is of interest to you and your business then contact your nailplate supplier technical representative (MiTek: Tim Rossiter, Pryda: Nick Cui, Multinail: Matthew Smith).
The new mid-rise timber market opportunity mightn’t be for everyone, the projects are comparatively taller and larger than traditional residential work, and they require higher levels of off-site prefabrication; but with this comes the opportunity for greater margins and new product innovation and supply.
Fabrication of prefabricated elements such as floor cassettes is actually fairly straight forward and doesn’t have to cost a lot of money for static based equipment set-up. They are also now becoming increasingly popular in the residential market for raised ground floor elements or upper storey floor systems. If you are interested in exploring floor cassette fabrication further for your residential jobs, then again contact your nailplate supplier technical representative as they have all the details now embedded in their software around floor cassette design and fabrication, and would be keen to meet with you to explain the opportunity.

4 storeys timber over concrete podium, Project: Oleo Apartments
Builder: Figurehead Constructions, F&T Sup: Timbertruss, Location: Mill Park, Vic
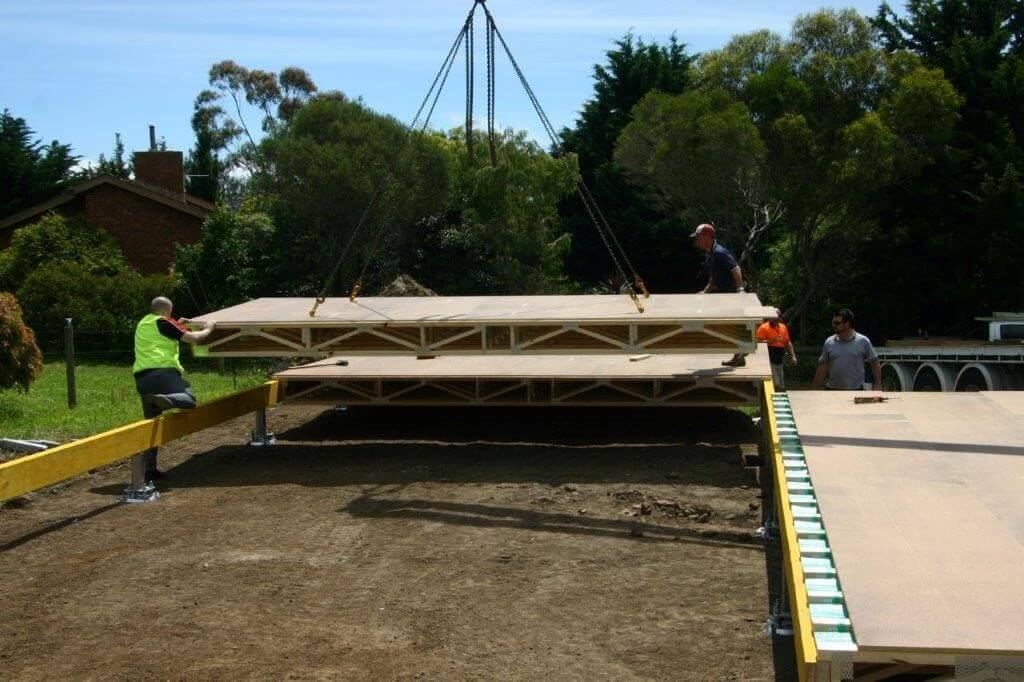
Ground floor cassette installation, F&T Sup: DWTT Future Fit, Location: Corinella, Vic