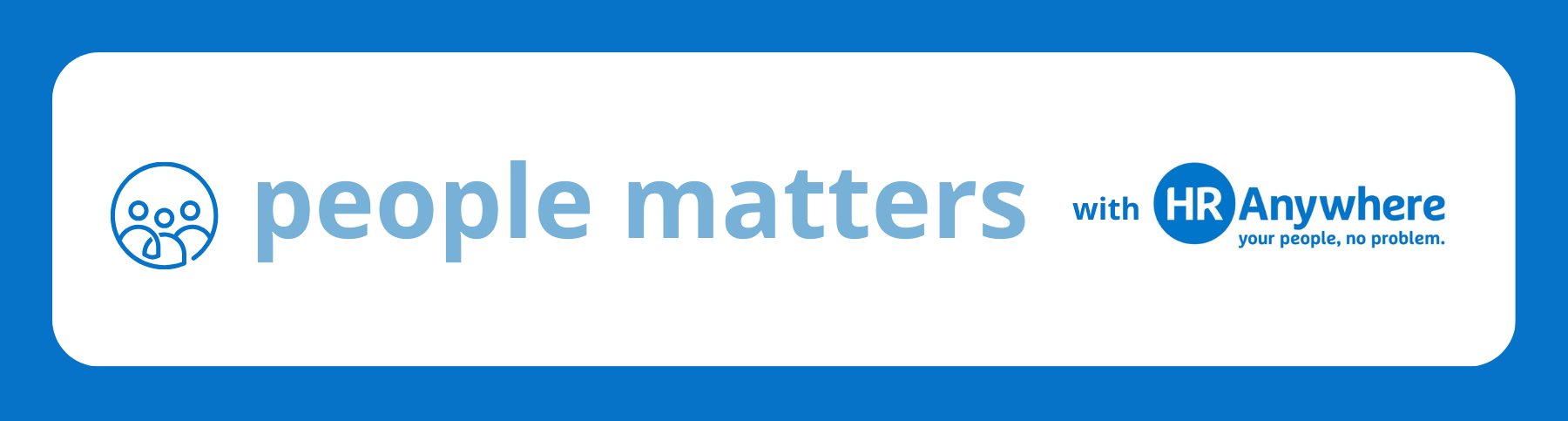
Safety Inductions – Plan carefully or pay a fine!
Big Bell Gold Operations Pty Ltd in WA was recently sentenced for failing to provide and maintain a safe working environment at its Bluebird gold processing plant in February 2020. Consequently, the company was ordered to pay a fine of $400,000 in addition to $6,000 in costs.
The breach occurred after a contract worker was injured performing a task that wasn’t covered in his one-hour online safety induction before working with a conveyor belt at the processing plant. Further to this, the workplace supervisor also had not received any training.
At the time of the offence, two workers were contracted to use tools to remove built up material from a conveyor, while it was running. One of the workers was using a shovel for this purpose when his left arm became entangled and was lacerated in a nip point between the belt and a return roller. Another worker pulled an emergency lanyard to stop the conveyor, and used a crowbar to lift the conveyor belt, allowing the trapped worker to remove his arm.
The Court found that while the conveyor belt was guarded, the guarding didn’t extend far enough towards the ground, leaving an 800-millimetre gap that workers could reach under to access hazardous moving parts. While the business has now extended the conveyor’s guarding and improving its safety training processes, the following key lessons were noted by the Worksafe WA Commission managing the case:
- Duty holders need to consult the WHS Code of Practice: Managing risks of plant in the workplace.
- Companies must ensure all workers have the required training and are assessed as competent on the tasks assigned to them.
It doesn’t matter what size your business is – you need to follow the relevant WHS Codes and train your staff accordingly!
Our Principal Partners

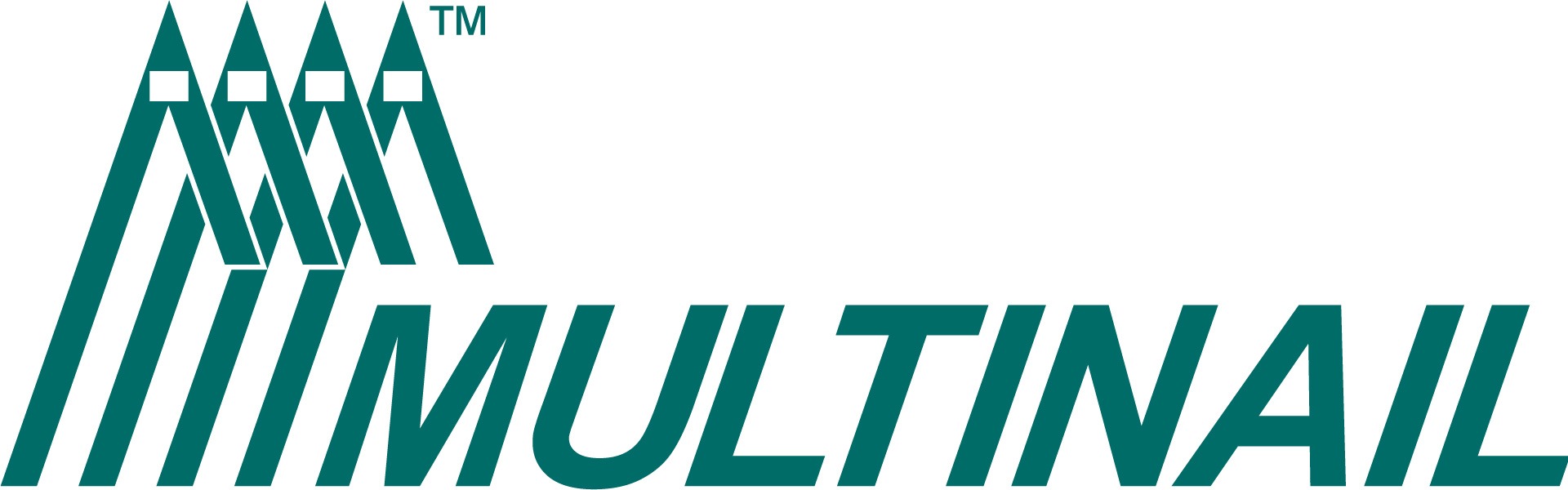
