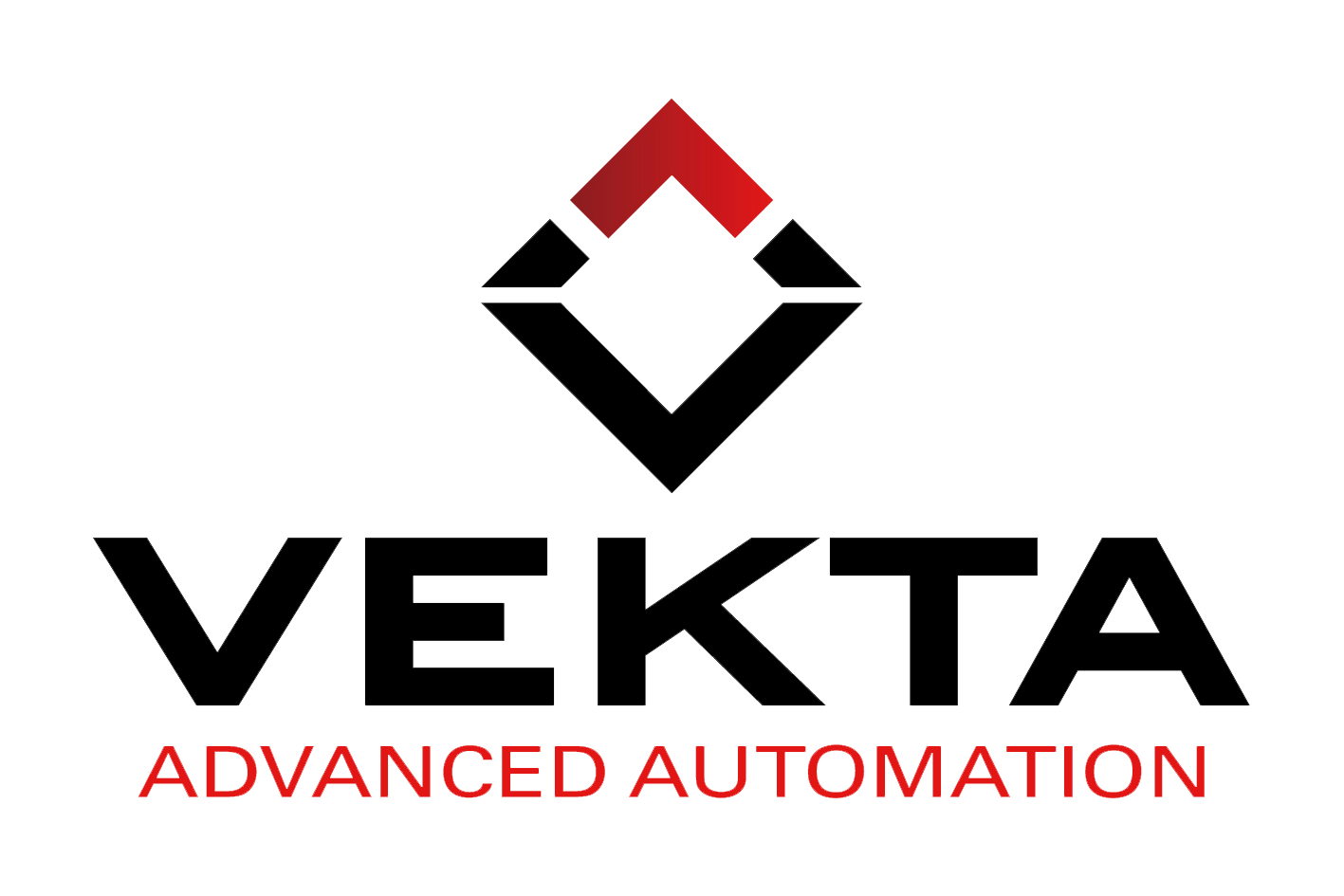
This piece was written and provided by FTMA Strategic Partner, Vekta Automation.
To meet the demands of modern construction, timber frame and truss manufacturers are embracing automation solutions. The automation revolution started with CNC linear saws for cutting and has now extended to the infeed of raw materials, the placing and nailing of plates and even stacking finished products. The main aim of the automation game- reduce the number of times a person touches the member.
Q: What does MC Hammer and a timber frame and truss plant have in common?
A: U can’t touch this!
From timber pack to infeed.
Outfeed to trolley.
Trolley to jig.
Jig to rollers.
Rollers to stack.
5 fairly common ‘touch’ points in a plant.
5 chances for slips, falls, chats or human error.
5 things that are completely avoidable thanks to automative solutions.
So, how can you MC Hammer this process?
Direct to station delivery with real time optimisation, also known as just-in-time delivery. A logistics strategy where cut members are delivered to the location needed at the exact time they are required. To implement that strategy- Vekta’s Direct Delivery System- DDS, coupled with Real Time Optimisation (RTO) software.
The Vekta DDS is a conveyor system that takes cut members from the outfeed directly to the assembly area as they are needed- with no touches (slips, falls, chats or human error) involved. In other words, the cut members ‘go with the flow’ and do ‘the bump’. Much of the logic takes place within the saw itself- optimising, orientation, order, and kickoff location considerations for example. The members are cut and then handed over to the DDS with the appropriate information. The DDS then flows the cut members, tracking them along the way, and bumping them off at the correct final location. The result, members are delivered to the jigs/assembly areas- in the correct orientation and order.
The Power of the Vekta RTO software facilitates this entire process; from raw timber to finished cut members delivered directly and can now be run by a single operator…with a tablet. Expert control over the prioritisation of jobs and workflow to the downstream stations, even recuts are no longer a problem, these are ordered with a jig/table side access screen and sent directly to the saw.
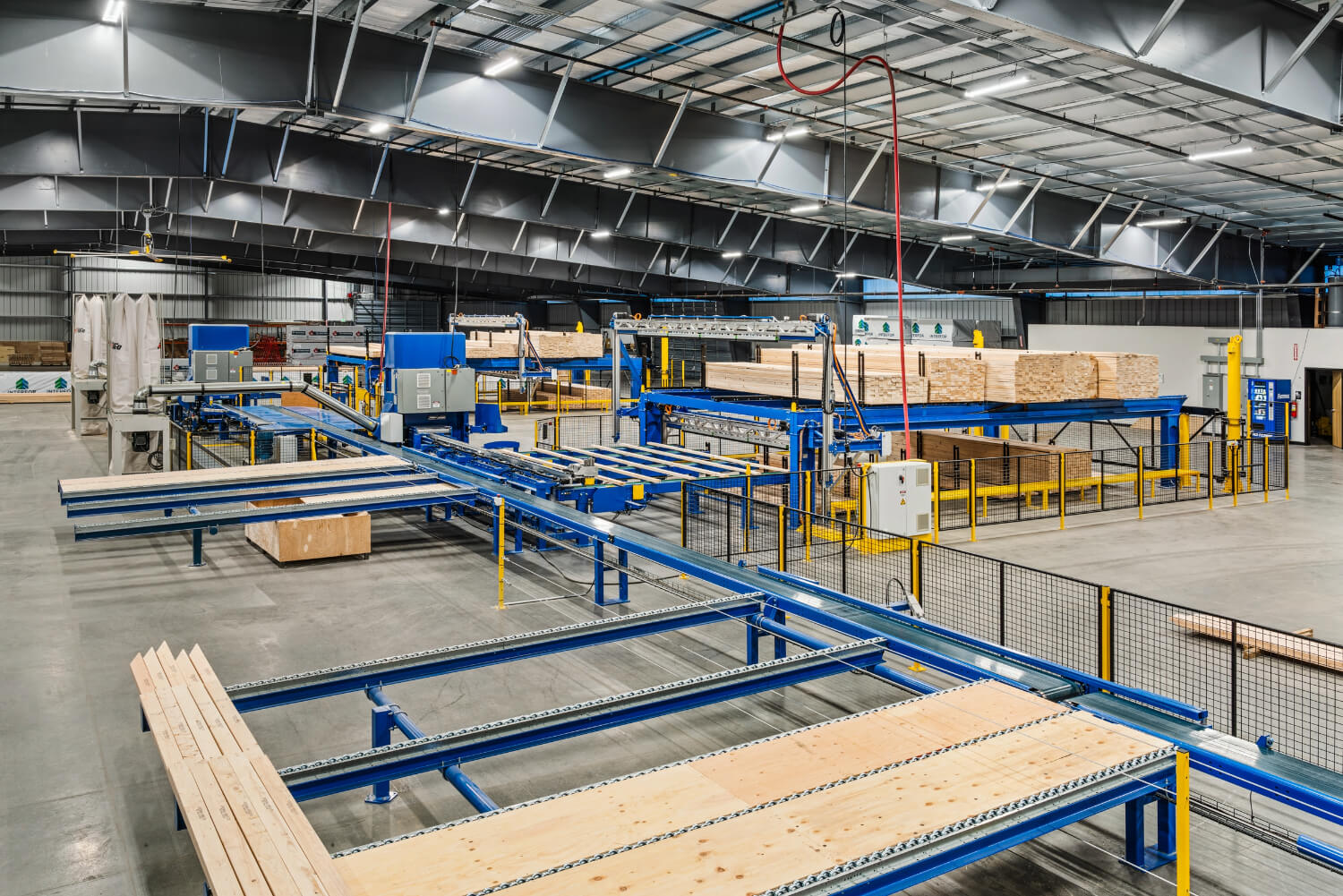
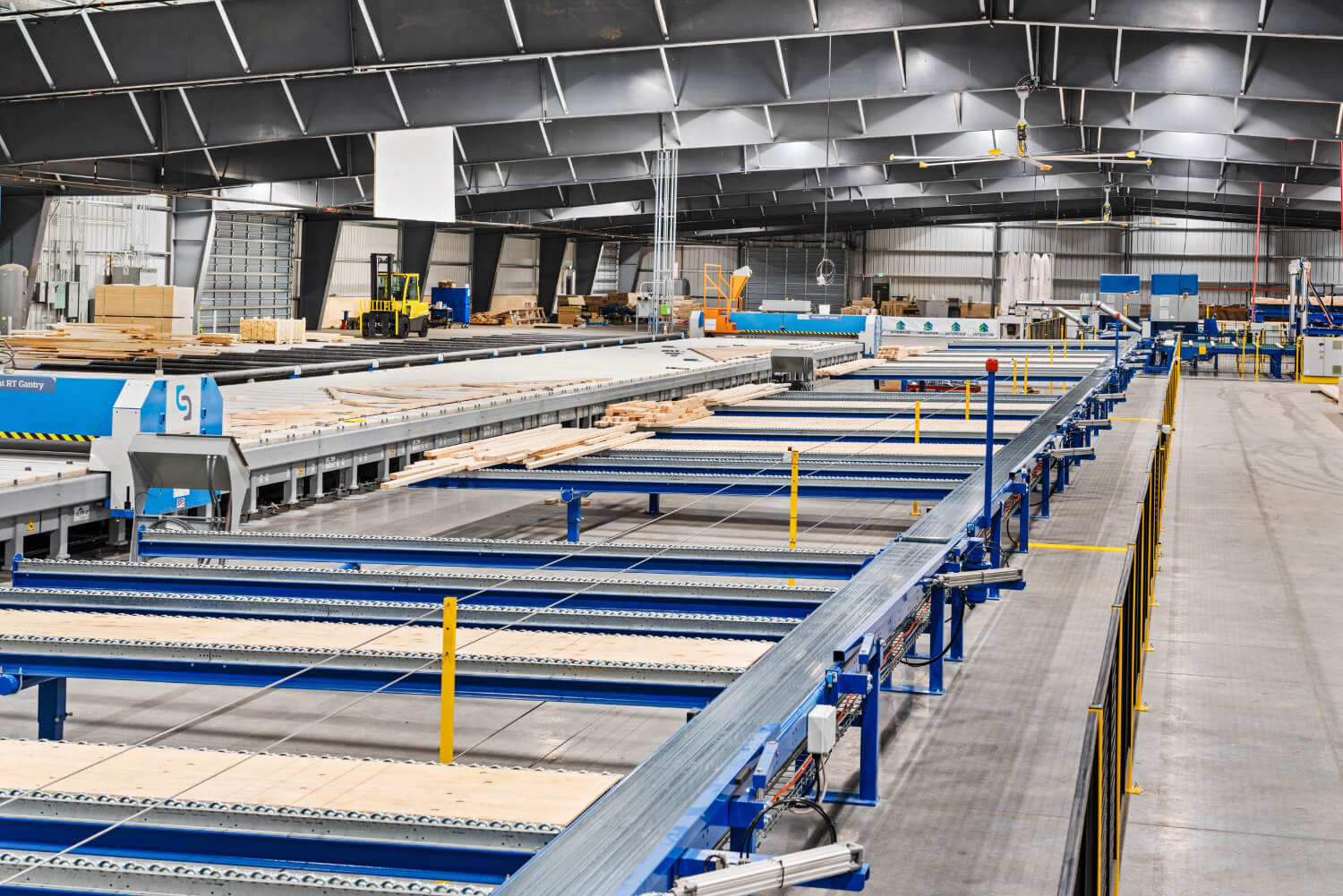
To ‘Break it down’
Every DDS is built bespoke to suit your site and needs, delivery in any direction at the correct orientation and with the correct justification.
The DDS accepts cut members from one or more saws without increasing needed operators, many saws working towards the jobs and prioritisations that are flexible and monitored.
Multiple handling, sawing and delivery solutions controlled by a single operator – what used to take a crew now only takes one general.
Easily maintained and repaired.
Keeping the staff you have, in the areas where they will provide the most value, is vital. Vekta Automation solutions remove the most labour intensive, least efficient steps in your plant. From pack handling, outfeed delivery to finished product movement and stacking Vekta can help you remove these added costs and risks from your plant by helping you embrace the ‘you can’t touch this’ mindset.
I told you
You can’t touch this
Too hype, you can’t touch this
Yo, Vekta outta here
You can’t touch this
Our Principal Partners

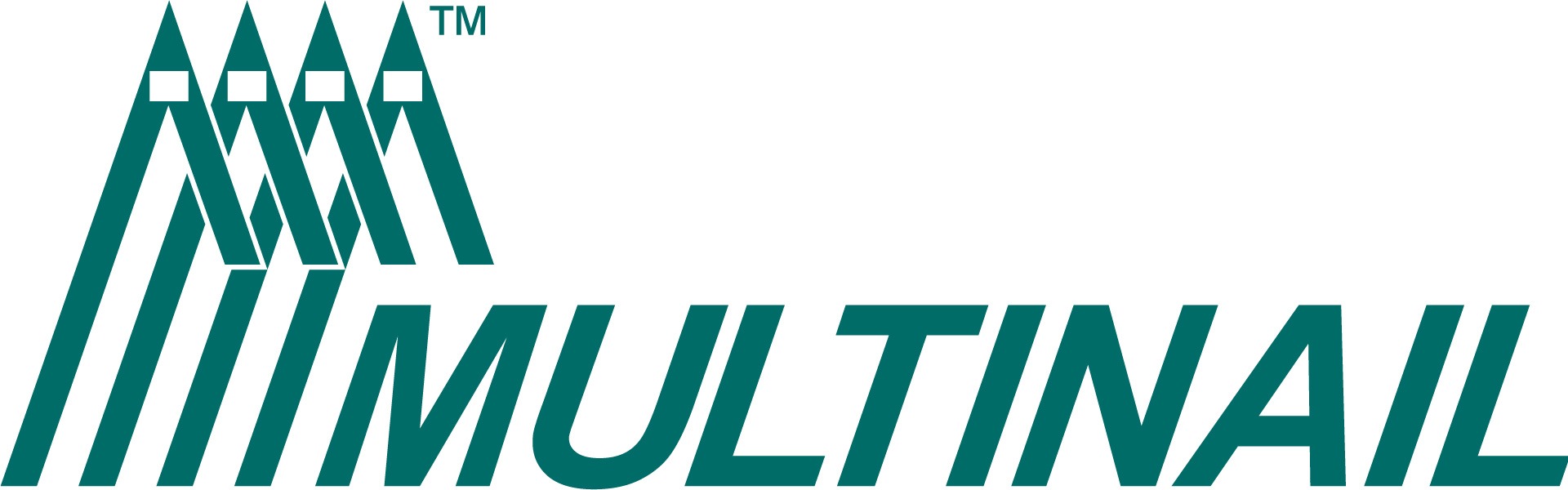
